Preparation method of composite foam concrete
A composite foam and concrete technology, applied in the field of building materials, can solve the problems of secondary processing such as difficult cutting of shaped concrete, accelerated decline in concrete strength, and affecting concrete strength, etc., to reduce production space, save energy, and have high porosity Effect
- Summary
- Abstract
- Description
- Claims
- Application Information
AI Technical Summary
Problems solved by technology
Method used
Image
Examples
Embodiment Construction
[0018] The scheme of the present invention will be described in detail below in conjunction with specific examples. This implementation case is based on the highest "strength-mass ratio" described in the previous background technology, and uses the "gradation" principle to repeatedly use the "highest strength-mass ratio" to obtain a higher "strength-mass ratio". ” of concrete, such as figure 1 Shown:
[0019] First, the water vapor is generated by the steam generator 3, and the air in the foam concrete mixer 2 is removed and filled with water vapor, and the air pressure is slightly higher than the external atmospheric pressure;
[0020] Further, by weight, 40 parts of Portland cement, 45 parts of superfine aggregate, 15 parts of fly ash, and 32 parts of water are imported into the ordinary concrete mixer 1 and stirred into concrete slurry. At this time, the volume of the concrete slurry for 1 copy;
[0021] Further, the concrete slurry with a volume of 1 part is introduced ...
PUM
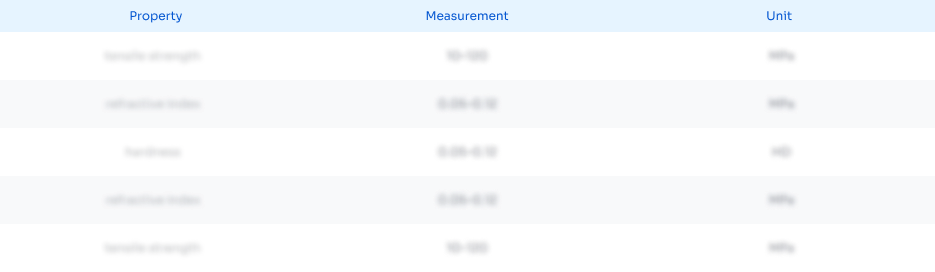
Abstract
Description
Claims
Application Information

- R&D Engineer
- R&D Manager
- IP Professional
- Industry Leading Data Capabilities
- Powerful AI technology
- Patent DNA Extraction
Browse by: Latest US Patents, China's latest patents, Technical Efficacy Thesaurus, Application Domain, Technology Topic, Popular Technical Reports.
© 2024 PatSnap. All rights reserved.Legal|Privacy policy|Modern Slavery Act Transparency Statement|Sitemap|About US| Contact US: help@patsnap.com