Part space size detection method
A detection method and technology of space size, applied in mechanical gap measurement, measurement device, mechanical measurement device, etc., can solve the problems of large error in detection results, affecting measurement efficiency, labor cost, etc., to achieve low cost and ensure accuracy , the effect of improving convenience
- Summary
- Abstract
- Description
- Claims
- Application Information
AI Technical Summary
Problems solved by technology
Method used
Image
Examples
Embodiment Construction
[0065] In order to make the purpose, technical solutions and advantages of the present invention clearer, the present invention will be further described in detail below in conjunction with the examples and accompanying drawings. As a limitation of the present invention.
[0066] In some embodiments, a method for detecting the space size of a part is provided, the part 1000 is as figure 1 The shown is usually a sheet metal structure, which is formed by stamping or manual bending. Specifically, a rectangular sheet metal part is bent on both sides to form the second included angle side 1000B in the middle and the second included angle The first angled side 1000A and the right-angled side 1000C at both ends of the side 1000B. The second angled side 1000B and the right angled side 1000C are perpendicular to each other, and the angle between the first angled side 1000A and the second angled side 1000B is not 90°. The intersection of the first angled side 1000A and the second angl...
PUM
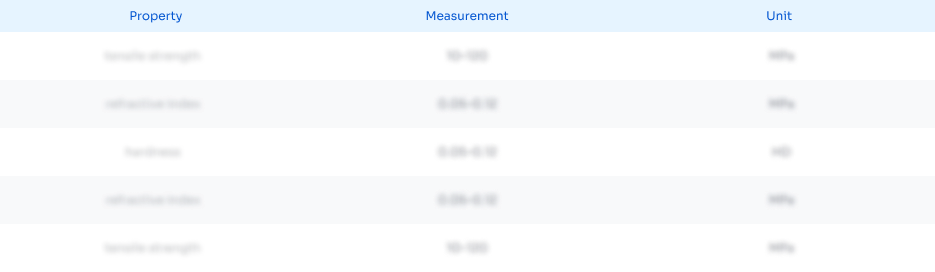
Abstract
Description
Claims
Application Information

- R&D Engineer
- R&D Manager
- IP Professional
- Industry Leading Data Capabilities
- Powerful AI technology
- Patent DNA Extraction
Browse by: Latest US Patents, China's latest patents, Technical Efficacy Thesaurus, Application Domain, Technology Topic, Popular Technical Reports.
© 2024 PatSnap. All rights reserved.Legal|Privacy policy|Modern Slavery Act Transparency Statement|Sitemap|About US| Contact US: help@patsnap.com