Non-circular gear dynamic contact characteristic analysis method based on tooth surface topological structure
A topology, non-circular gear technology, used in special data processing applications, instruments, electrical digital data processing, etc.
- Summary
- Abstract
- Description
- Claims
- Application Information
AI Technical Summary
Problems solved by technology
Method used
Image
Examples
Embodiment Construction
[0042] In order to make the object, technical solution and advantages of the present invention clearer, the present invention will be further described in detail below in conjunction with the accompanying drawings and embodiments.
[0043] This embodiment provides a method for analyzing the dynamic contact characteristics of non-circular gears based on tooth surface topology, including the following steps:
[0044] Step 1: Design non-circular gear pair in KISSsoft, input parameters: modulus m=3, number of teeth z1=z2=47, pressure angle α=20°, tooth width b=30, pitch curve equation r=64.667 / 1-0.3287 cos(θ), after setting parameters, generate as figure 2 The two-dimensional model of the non-circular gear pair shown; save the two-dimensional model of the non-circular gear pair in iges format.
[0045] Step 2: Import the iges format file generated in step 1 into Creo, create a new part, and stretch the imported 2D model of the non-circular gear pair. The stretching height is 30m...
PUM
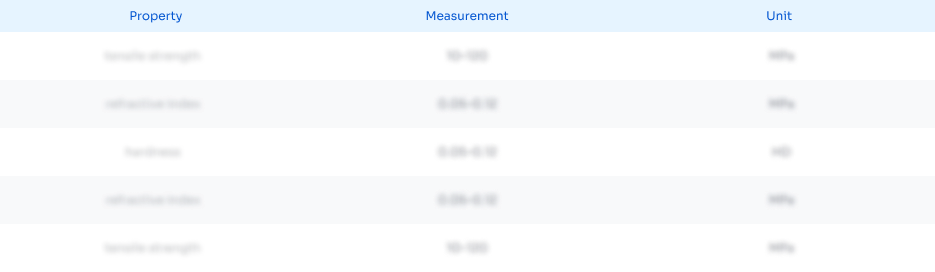
Abstract
Description
Claims
Application Information

- R&D Engineer
- R&D Manager
- IP Professional
- Industry Leading Data Capabilities
- Powerful AI technology
- Patent DNA Extraction
Browse by: Latest US Patents, China's latest patents, Technical Efficacy Thesaurus, Application Domain, Technology Topic, Popular Technical Reports.
© 2024 PatSnap. All rights reserved.Legal|Privacy policy|Modern Slavery Act Transparency Statement|Sitemap|About US| Contact US: help@patsnap.com