Aluminum silicate glass ion coloring agent and colored aluminum silicate glass thereof
A technology of aluminosilicate glass and coloring agent, which is applied in the field of glass manufacturing, and can solve the problems of particle size, thickness and uniformity of slurry, influence of ion diffusion effect, single color, etc.
- Summary
- Abstract
- Description
- Claims
- Application Information
AI Technical Summary
Problems solved by technology
Method used
Image
Examples
Embodiment 1
[0016] Embodiment 1: This embodiment provides an ionic colorant and glass using the ionic colorant,
[0017] Original glass with thickness of 0.7mm, composition is SiO 2 65wt%, Al 2 O 3 13wt%, Na 2 O13wt%, K 2 O5wt%, MgO3wt%, B2O31wt%.
[0018] The glass was cleaned and placed in a preheating furnace at 250° C. for preheating for 10 minutes, and then placed in the molten ionic colorant composed of Table 1 for ion diffusion. After the ion diffusion is completed, the glass is taken out and placed in an annealing furnace at 260°C, cooled to room temperature, and taken out, and washed to obtain a light yellow finished product.
Embodiment 2
[0019] Embodiment 2: This embodiment provides an ionic colorant and glass using the ionic colorant,
[0020] Original glass with thickness of 0.7mm, composition is SiO 2 67wt%, Al 2 O 3 12wt%, Na 2 O12wt%, K 2 O5wt%, MgO3wt%, B2O31wt%. The glass was cleaned and placed in a preheating furnace at 260°C for preheating for 20 minutes, and then placed in the molten ionic colorant composed of Table 1 for ion diffusion. After the ion diffusion is completed, the glass is taken out and placed in an annealing furnace at 300°C, cooled to room temperature, taken out, and washed to obtain a reddish brown finished product.
Embodiment 3
[0021] Embodiment 3: This embodiment provides an ionic colorant and glass using the ionic colorant,
[0022] Original glass with thickness of 0.55mm, composition is SiO 2 66wt%, Al 2 O 3 15wt%, Na 2 O13wt%, K 2 O3wt%, MgO3wt%. The glass was cleaned and placed in a preheating furnace at 220°C for preheating for 10 minutes, and then placed in the molten ionic colorant composed of Table 1 for ion diffusion. After the ion diffusion is completed, the glass is taken out and placed in an annealing furnace at 300°C, cooled to room temperature, taken out, and washed to obtain a light yellow finished product.
[0023] Table 1 is the composition, process parameters and color table of the ionic colorant of Example 1-3
[0024]
PUM
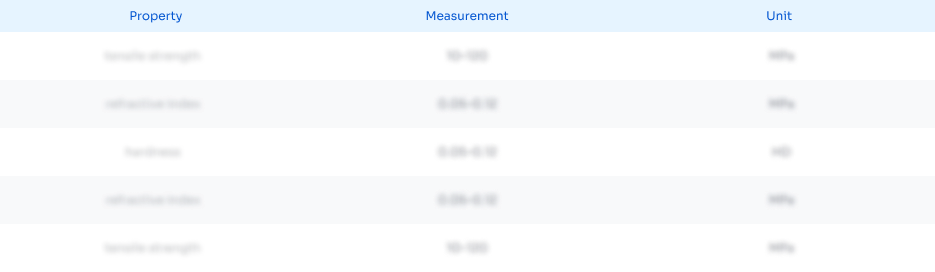
Abstract
Description
Claims
Application Information

- Generate Ideas
- Intellectual Property
- Life Sciences
- Materials
- Tech Scout
- Unparalleled Data Quality
- Higher Quality Content
- 60% Fewer Hallucinations
Browse by: Latest US Patents, China's latest patents, Technical Efficacy Thesaurus, Application Domain, Technology Topic, Popular Technical Reports.
© 2025 PatSnap. All rights reserved.Legal|Privacy policy|Modern Slavery Act Transparency Statement|Sitemap|About US| Contact US: help@patsnap.com