Robot calibration system, two-dimensional plane motion calibration method and three-dimensional space motion calibration method
A technology for calibrating systems and robots, applied in the field of robotics
- Summary
- Abstract
- Description
- Claims
- Application Information
AI Technical Summary
Problems solved by technology
Method used
Image
Examples
Embodiment
[0190] In this embodiment, taking the prism assembly 31 as a double prism as an example, the two-dimensional plane motion calibration method of the system is as follows:
[0191] a1. Establish the world coordinate system O w -X w Y w Z w , establish the robot coordinate system O R -X R Y R Z R , establish the measurement component coordinate system O M -X M Y M Z M , establish the coordinate system O of the prism component in the measurement component 3 r -X r Y r Z r , set up the camera coordinate system O matched with the prism assembly 31 c -X c Y c Z c , will measure the component coordinate system O M -X M Y M Z M , the world coordinate system O w -X w Y w Z w And the camera coordinate system O matched with the measurement component 3 c -X c Y c Z c ;
[0192] a2. The host computer 4 controls the prism assembly 31 of the measurement assembly 3, so that the visual axis of the camera 32 passes through the prism assembly 31 without deflection, a...
PUM
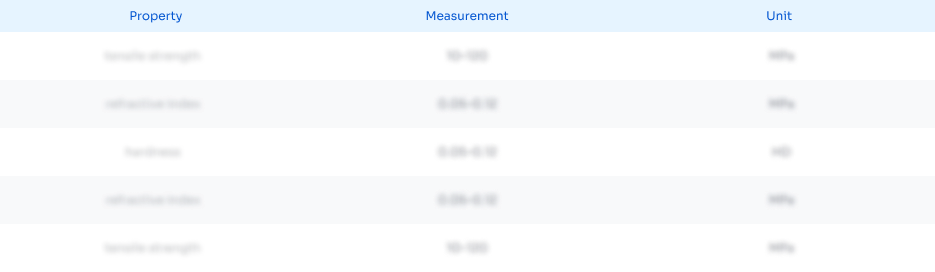
Abstract
Description
Claims
Application Information

- R&D Engineer
- R&D Manager
- IP Professional
- Industry Leading Data Capabilities
- Powerful AI technology
- Patent DNA Extraction
Browse by: Latest US Patents, China's latest patents, Technical Efficacy Thesaurus, Application Domain, Technology Topic, Popular Technical Reports.
© 2024 PatSnap. All rights reserved.Legal|Privacy policy|Modern Slavery Act Transparency Statement|Sitemap|About US| Contact US: help@patsnap.com