Unpowered ink mixing process for label printing
A label printing and ink technology, which is applied to the general parts of printing machinery, printing, printing machines, etc., can solve problems such as assembly difficulties and lower ink quality, and achieve the effects of avoiding precipitation, improving quality, and increasing the amount of gasification
- Summary
- Abstract
- Description
- Claims
- Application Information
AI Technical Summary
Problems solved by technology
Method used
Image
Examples
Embodiment
[0024] refer to Figure 1-2 , a non-powered ink mixing process for label printing, comprising the following steps:
[0025] S1: The preparation of the flexographic printing plate is realized through back exposure, main exposure, washing, drying and post-processing.
[0026] S2: Put the printing plate into the printing machine, fill the equipment with enough ink, and start label printing.
[0027] S3: Arranging, drying, and flattening the printed labels, and then slicing them into predetermined shapes and sizes.
[0028] S4: Carry out label defect detection, and remove labels with problems such as character defects, dirt, missing characters, and typos through testing equipment;
[0029] The above process still uses the following equipment, including the ink storage tank 1, the bottom of the ink storage tank 1 is fixedly connected with the fixed table 2, the bottom of the ink storage tank 1 is provided with a discharge port, the discharge port is sealed and connected with a di...
PUM
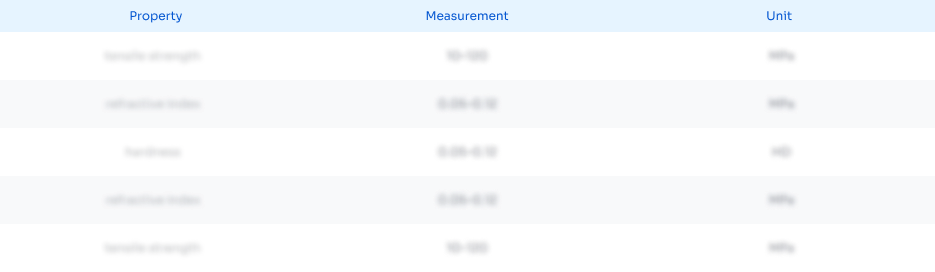
Abstract
Description
Claims
Application Information

- R&D
- Intellectual Property
- Life Sciences
- Materials
- Tech Scout
- Unparalleled Data Quality
- Higher Quality Content
- 60% Fewer Hallucinations
Browse by: Latest US Patents, China's latest patents, Technical Efficacy Thesaurus, Application Domain, Technology Topic, Popular Technical Reports.
© 2025 PatSnap. All rights reserved.Legal|Privacy policy|Modern Slavery Act Transparency Statement|Sitemap|About US| Contact US: help@patsnap.com