Pneumatic-electric hybrid force control end effector for robot
An end effector and hybrid technology, which is applied in the direction of grinding machine parts, workpiece feed movement control, grinding frame, etc., can solve the problem of not meeting the requirements of real-time rapid force control and the small range of force adjustment , easy to produce vibration and other problems, to achieve the effect of large force-to-weight ratio, large force control adjustment range, and low production cost
- Summary
- Abstract
- Description
- Claims
- Application Information
AI Technical Summary
Problems solved by technology
Method used
Image
Examples
Embodiment Construction
[0028] The present invention will be further described in detail below in conjunction with the embodiments and the accompanying drawings. It should be noted that the following embodiments are intended to facilitate understanding of the present invention, but do not limit it in any way.
[0029] In this embodiment, the gas-electric hybrid force-controlled end effector includes a fixed platform 2 articulated with the end of the mechanical arm, and a movable platform 10 that can move relative to the fixed platform 2 through a guide device 4 . Between the moving platform 10 and the fixed platform 2, an air telescopic spring 6 and a linear motor arranged in parallel are arranged to drive the moving platform 10 to move axially along the guide device 4. The guide device 4 is provided with a displacement sensor 5 for detecting the moving position of the moving platform 10, the moving platform 10 is provided with a pressure sensor 11 and an inclination sensor 12, the displacement sensor...
PUM
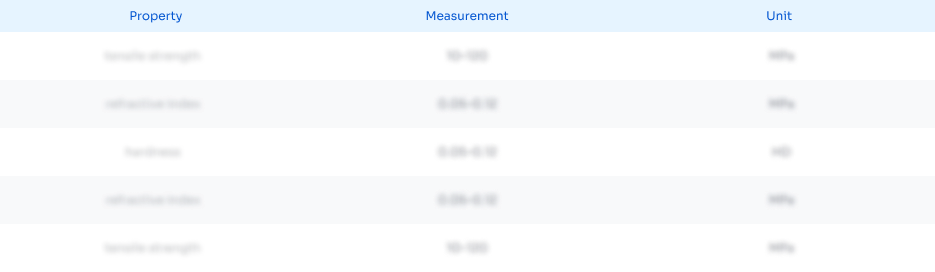
Abstract
Description
Claims
Application Information

- R&D Engineer
- R&D Manager
- IP Professional
- Industry Leading Data Capabilities
- Powerful AI technology
- Patent DNA Extraction
Browse by: Latest US Patents, China's latest patents, Technical Efficacy Thesaurus, Application Domain, Technology Topic, Popular Technical Reports.
© 2024 PatSnap. All rights reserved.Legal|Privacy policy|Modern Slavery Act Transparency Statement|Sitemap|About US| Contact US: help@patsnap.com