Preparation method and application of high-dispersion metal oxide/carbon nanofiber composite material
A technology of carbon nanofibers and composite materials, applied in the direction of active material electrodes, electrochemical generators, electrical components, etc., can solve the problems of agglomeration or pulverization, low dispersion, large metal oxide particles, etc., and achieve low cost, The effect of simple process and high sodium storage capacity
- Summary
- Abstract
- Description
- Claims
- Application Information
AI Technical Summary
Problems solved by technology
Method used
Image
Examples
Embodiment 1
[0033] The preparation method of material among the present invention is as follows successively:
[0034] (1) According to the mass ratio of polyvinylpyrrolidone: ferrous acetate: polyacrylonitrile: dimethylformamide solution is 1:1:1:10, take the material, stir well and evenly to obtain the spinning stock solution;
[0035] (2) Take the above-mentioned spinning stock solution and place it in the propeller for electrospinning operation, set the electrospinning process parameters to control the voltage at 13kV, the advance rate of the precursor solution is 0.5mL / h, and the receiving distance is 13cm, and then the fiber film is obtained;
[0036] (3) The fiber film was placed in a tube furnace, and under nitrogen atmosphere, the temperature was raised to 800°C at 2°C / min, and the carbonization heat treatment was carried out for 2h, so as to obtain a highly dispersed ferric oxide / carbon nanofiber composite material.
Embodiment 2
[0038] (1) According to the mass ratio of polyvinylpyrrolidone: ferric nitrate: polyacrylonitrile: dimethylformamide solution is 1:1:1:10, take the material, stir fully and evenly to obtain the spinning stock solution;
[0039] (2) Take the above-mentioned spinning stock solution and place it in the propeller for electrospinning operation, set the electrospinning process parameters to control the voltage at 13kV, the advance rate of the precursor solution is 0.5mL / h, and the receiving distance is 13cm, and then the fiber film is obtained;
[0040] (3) The fiber film was placed in a tube furnace, and under nitrogen atmosphere, the temperature was raised to 800°C at 2°C / min, and the carbonization heat treatment was carried out for 2h, so as to obtain a highly dispersed ferric oxide / carbon nanofiber composite material.
Embodiment 3
[0042] (1) According to the mass ratio of polyvinylpyrrolidone: ferric chloride: polyacrylonitrile: dimethylformamide solution is 1:1:1:10, take materials, stir fully and evenly to obtain spinning stock solution;
[0043] (2) Take the above-mentioned spinning stock solution and place it in the propeller for electrospinning operation, set the electrospinning process parameters to control the voltage at 13kV, the advance rate of the precursor solution is 0.5mL / h, and the receiving distance is 13cm, and then the fiber film is obtained;
[0044] (3) The fiber film was placed in a tube furnace, and under nitrogen atmosphere, the temperature was raised to 800°C at 2°C / min, and the carbonization heat treatment was carried out for 2h, so as to obtain a highly dispersed ferric oxide / carbon nanofiber composite material.
PUM
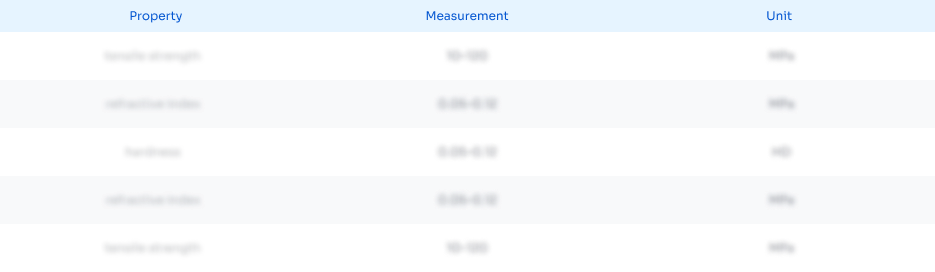
Abstract
Description
Claims
Application Information

- R&D
- Intellectual Property
- Life Sciences
- Materials
- Tech Scout
- Unparalleled Data Quality
- Higher Quality Content
- 60% Fewer Hallucinations
Browse by: Latest US Patents, China's latest patents, Technical Efficacy Thesaurus, Application Domain, Technology Topic, Popular Technical Reports.
© 2025 PatSnap. All rights reserved.Legal|Privacy policy|Modern Slavery Act Transparency Statement|Sitemap|About US| Contact US: help@patsnap.com