Novel dual-blade-groove cutting tool
A new type of cutting edge technology, applied in the field of mechanical parts processing, can solve the problems of inability to complete normal processing, large tool width contact surface, large processing vibration, etc., to solve the problems of tool chatter, improved tool durability and low processing efficiency. Effect
- Summary
- Abstract
- Description
- Claims
- Application Information
AI Technical Summary
Problems solved by technology
Method used
Image
Examples
Embodiment 1
[0038] This embodiment provides a novel double-edged groove cutter, comprising a knife bar 1 and two profiled blades 2 with identical structures and sizes, and the two profiled blades 2 are installed on the same working plane at the end of the knife bar 1; One of the profiling blades 2 has an angle α to the left of the main knife edge at the working end, and the other profiling blade 2 has an angle α to the right of the main knife edge at the working end, and the two profiling blades 2 are symmetrically distributed in left and right mirror images, where α is an acute angle , the main cutting edges of the working ends of the two profiling blades 2 are located on a straight line in the plane. The groove cutter is used to machine the inner ring groove of the long axis parts.
Embodiment 2
[0040] Further improvement on the basis of Example 1, the angle α is equal to 35°, that is, one profiling blade 2 deviates to the left by 35°, and the other profiling blade 2 deviates to the right by 35°; both profiling blades 2 pass through the screw 3 It is fixed on the same working surface at the end of the tool bar 1. Specifically, a through hole is provided at the geometric center of the two profiling blades 2. After the screw 3 passes through the through hole, it is threaded and fixed on the same working surface at the end of the tool bar 1. work surface.
Embodiment 3
[0042]As a further improvement on the basis of Embodiment 2, a mounting groove 4 is opened on a working surface at the end of the cutter bar 1, and two profiling blades 2 are inserted into the mounting grooves to be fixed. The adjacent two side walls away from the free end of the tool bar 1 on the mounting groove 4 are V-shaped structures, and the inner bottom surface of the mounting groove 4 is protruded with a wedge-shaped limiter I5 and a wedge-shaped limiter II6, and the wedge-shaped limiter I5 and the wedge-shaped limiter The position piece II6 is located on the center line of the mirror image of the two profiling blades 2; the two side walls of the non-working end of the main knife edge of one of the profiling blades 2 are respectively connected to the side wall of the V-shaped structure and one side of the wedge-shaped stopper I5 The inclined walls are in contact with each other, and the side wall of the main knife edge of the working end of the profiling blade 2 protrud...
PUM
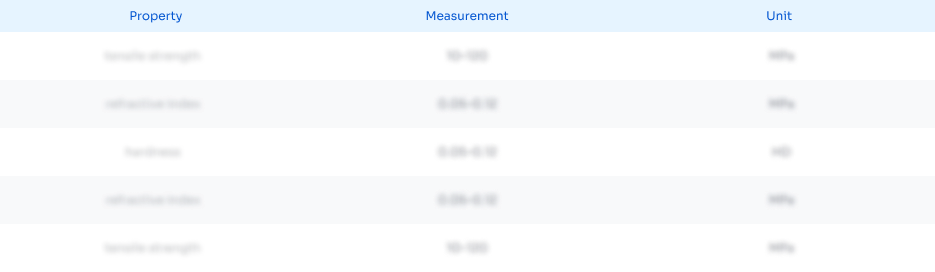
Abstract
Description
Claims
Application Information

- R&D
- Intellectual Property
- Life Sciences
- Materials
- Tech Scout
- Unparalleled Data Quality
- Higher Quality Content
- 60% Fewer Hallucinations
Browse by: Latest US Patents, China's latest patents, Technical Efficacy Thesaurus, Application Domain, Technology Topic, Popular Technical Reports.
© 2025 PatSnap. All rights reserved.Legal|Privacy policy|Modern Slavery Act Transparency Statement|Sitemap|About US| Contact US: help@patsnap.com