Vertical Differential Velocity Measuring Method of Test Pull Coordinate System
A technology of coordinate system and test piece, applied in the field of optical measurement, can solve problems such as low efficiency, time-consuming, affecting detection and production progress, etc., and achieve the effect of high reliability, accurate method, and meeting the precision requirements of the machine itself
- Summary
- Abstract
- Description
- Claims
- Application Information
AI Technical Summary
Problems solved by technology
Method used
Image
Examples
specific Embodiment approach 1
[0036] Specific embodiment one: the vertical differential velocity measuring method of test pull piece coordinate system, it comprises the following steps:
[0037] Step 1: Fix the workpiece on the three-dimensional optical measuring instrument,
[0038] Step 2: Optically position the workpiece and set up a coordinate system,
[0039] Use any right angle in the square hole in the middle of the workpiece as the starting position of the coordinate system to locate and establish the coordinate system;
[0040] Step 3: Manually call the probe mode to measure the vertical difference of the workpiece,
[0041] Call the probe, manually measure four points on the rectangular plane of the square hole in the middle of the workpiece, determine the measured range of the measuring surface, use the three-dimensional optical measuring instrument to build a rectangular grid, and the machine will automatically distribute the measurement in the form of a grid within the determined range of the...
specific Embodiment approach 2
[0044] Specific implementation mode two: the specific process of setting up the coordinate system in the step two is as follows: two right-angled sides extending at right angles from the starting position are used as reference lines, one is used as the X axis, and the other is used as the Y axis; Point fitting plane, set the Z axis to be perpendicular to the plane.
[0045] Other implementation manners are the same as the specific implementation manner 1.
specific Embodiment approach 3
[0046] Embodiment 3: The process of building a rectangular network of the three-dimensional optical measuring instrument in step three is: using the automatic measurement path and coordinate grid function of the three-dimensional optical measuring instrument to construct.
[0047] Other implementation manners are the same as the specific implementation manner 1.
PUM
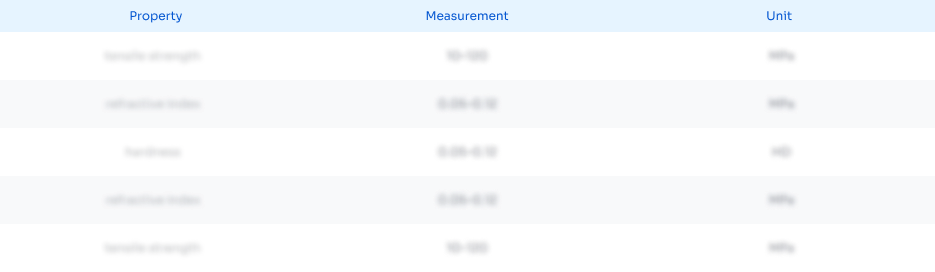
Abstract
Description
Claims
Application Information

- Generate Ideas
- Intellectual Property
- Life Sciences
- Materials
- Tech Scout
- Unparalleled Data Quality
- Higher Quality Content
- 60% Fewer Hallucinations
Browse by: Latest US Patents, China's latest patents, Technical Efficacy Thesaurus, Application Domain, Technology Topic, Popular Technical Reports.
© 2025 PatSnap. All rights reserved.Legal|Privacy policy|Modern Slavery Act Transparency Statement|Sitemap|About US| Contact US: help@patsnap.com