Variable-stiffness exoskeleton structure based on positive pressure friction principle
A variable stiffness, exoskeleton technology, used in physical therapy, program-controlled manipulators, passive exercise equipment, etc., can solve the problems of heavy weight, large volume, and low practical value, and achieve easy control, small size, and structure. simple effect
- Summary
- Abstract
- Description
- Claims
- Application Information
AI Technical Summary
Problems solved by technology
Method used
Image
Examples
Embodiment Construction
[0019] The present invention will be described in further detail below in conjunction with the accompanying drawings and specific embodiments. It should be understood that the specific embodiments described here are only used to explain the present invention, not to limit the present invention.
[0020] Such as Figure 1-3 As shown, the variable stiffness exoskeleton structure of the present invention based on the principle of positive pressure friction includes a C-shaped tube 1, a fixing ring 2, a sleeve 3, a connecting rod 4, an inner hexagon screw 5, a silicone rubber tube 6 and a retaining ring 7; The principle of positive pressure friction means that the expansion of the silicone rubber tube after inflation increases the pressure and friction between the C-shaped tube and the sleeve, thereby realizing the variable stiffness of the joint; the C-shaped tube is a cross-section similar to For the C-shaped aluminum alloy tube, there is a threaded hole opposite to the opening...
PUM
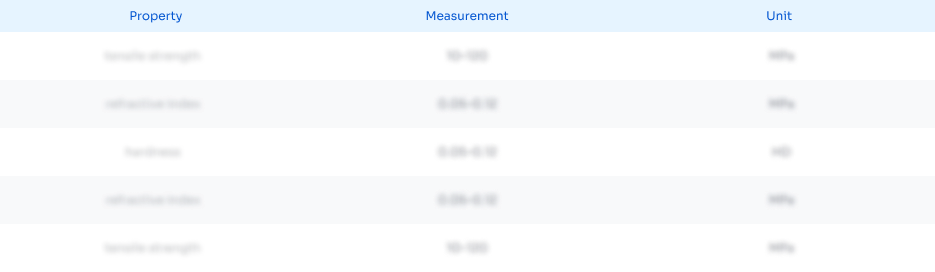
Abstract
Description
Claims
Application Information

- R&D
- Intellectual Property
- Life Sciences
- Materials
- Tech Scout
- Unparalleled Data Quality
- Higher Quality Content
- 60% Fewer Hallucinations
Browse by: Latest US Patents, China's latest patents, Technical Efficacy Thesaurus, Application Domain, Technology Topic, Popular Technical Reports.
© 2025 PatSnap. All rights reserved.Legal|Privacy policy|Modern Slavery Act Transparency Statement|Sitemap|About US| Contact US: help@patsnap.com