Multi-objective intelligent optimization design method for underground coal mine unmanned aerial vehicle structure
A technology of multi-objective optimization and design method, which is applied in the field of multi-objective intelligent optimization design of unmanned aerial vehicles in coal mines, to achieve the effects of ensuring smooth implementation, reducing computing costs, and improving effectiveness
- Summary
- Abstract
- Description
- Claims
- Application Information
AI Technical Summary
Problems solved by technology
Method used
Image
Examples
Embodiment 1
[0090] Embodiment 1: the multi-objective intelligent optimization design method of unmanned aerial vehicle structure in coal mine, it is characterized in that, comprises the steps:
[0091] Step 1) Select the key parameters of the UAV frame and power system, determine the decision variables for the UAV structure optimization in the coal mine, and determine the variable type and value range.
[0092] Step 2) Use the Latin hypercube sampling method, combined with the Fluent numerical simulation software, to generate a sample data set of the UAV structure and its lift.
[0093] Step 3) An ensemble learning model consisting of the Kriging method and radial basis functions is used to establish a lift proxy model for the UAV structure scheme in the coal mine.
[0094] Step 4) Taking into account the three optimization objectives of UAV quality, lift and cost, a three-objective optimization design model for the UAV structure in coal mines is established.
[0095] Step 5) Use the mul...
PUM
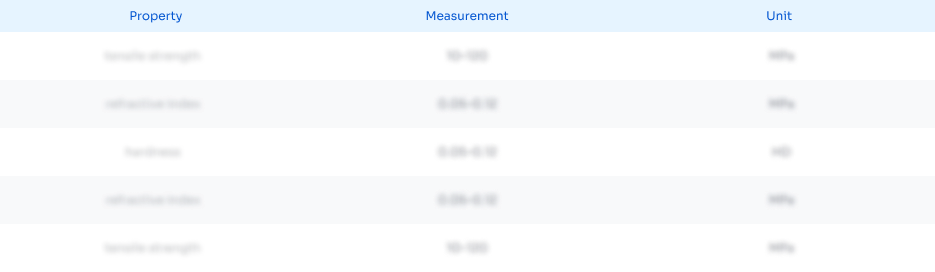
Abstract
Description
Claims
Application Information

- R&D Engineer
- R&D Manager
- IP Professional
- Industry Leading Data Capabilities
- Powerful AI technology
- Patent DNA Extraction
Browse by: Latest US Patents, China's latest patents, Technical Efficacy Thesaurus, Application Domain, Technology Topic, Popular Technical Reports.
© 2024 PatSnap. All rights reserved.Legal|Privacy policy|Modern Slavery Act Transparency Statement|Sitemap|About US| Contact US: help@patsnap.com