A Compensation Method for Spatial Positioning Error Based on Siemens System
A technology of spatial positioning and error compensation, applied in the field of CNC machine tools, can solve the problems of inability to cover the spatial positioning accuracy error term of machine tools and high compensation accuracy, and achieve the effect of improving spatial positioning accuracy, accurate compensation accuracy and processing accuracy.
- Summary
- Abstract
- Description
- Claims
- Application Information
AI Technical Summary
Problems solved by technology
Method used
Image
Examples
Embodiment 1
[0049] As the basic implementation mode of the present invention, the present invention includes a kind of spatial positioning error compensation method based on Siemens system, comprising the following steps:
[0050] a. Construct the mapping relationship between the geometric error of each feed axis of the five-axis CNC machine tool and the tool space positioning error, establish the geometric error model of the five-axis CNC machine tool, and provide a mathematical basis for the compensation of space positioning errors;
[0051] b. Identify the various geometric errors of the feed axis of the machine tool, bring them into the geometric error model established in step a, establish a spatial positioning error prediction model, and predict the spatial positioning error of the five-axis CNC machine tool, which is the spatial positioning error Compensation provides direct guidance;
[0052] c. Combining the spatial positioning error prediction model and the sag error compensation ...
Embodiment 2
[0054] The five-axis CNC machine tool is composed of three translational axes and two swinging axes. According to the combination sequence of the translational axes and the swinging axes, five-axis machine tools with different topological structures will be produced. These five-axis machine tools can realize complex five-degree-of-freedom machining. Among them, the mobile gantry five-axis CNC machine tool has a large span and a long processing stroke, which is most suitable for processing large and complex structural parts. It has a large working space and high processing accuracy requirements. There is a strong demand for positioning error compensation. As the best implementation mode of the present invention, the present invention is aimed at the compensation of space positioning error of the mobile gantry type five-axis machine tool, which specifically includes: geometric error modeling of the five-axis CNC machine tool, prediction of the space positioning error of the five-...
PUM
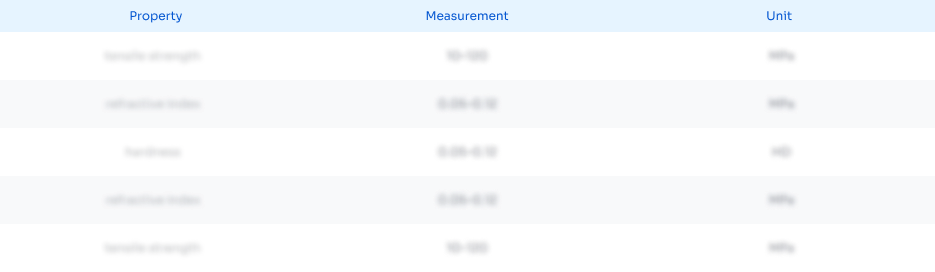
Abstract
Description
Claims
Application Information

- Generate Ideas
- Intellectual Property
- Life Sciences
- Materials
- Tech Scout
- Unparalleled Data Quality
- Higher Quality Content
- 60% Fewer Hallucinations
Browse by: Latest US Patents, China's latest patents, Technical Efficacy Thesaurus, Application Domain, Technology Topic, Popular Technical Reports.
© 2025 PatSnap. All rights reserved.Legal|Privacy policy|Modern Slavery Act Transparency Statement|Sitemap|About US| Contact US: help@patsnap.com