High-low type dual-vortex-chamber dual-necking combustion chamber
A combustion chamber, double swirl technology, applied in engine components, machines/engines, pistons, etc., can solve problems such as reducing the average temperature in the cylinder, and achieve the effect of reducing NOx and SOOT
- Summary
- Abstract
- Description
- Claims
- Application Information
AI Technical Summary
Problems solved by technology
Method used
Image
Examples
specific Embodiment approach 1
[0029] Such as figure 1 Shown: a high and low double vortex chamber double constriction combustion chamber, the longitudinal section of the combustion chamber is butterfly-shaped, the combustion chamber is divided into two arc-shaped constriction vortex chambers distributed up and down, and the center of the combustion chamber is the arc top Round table.
[0030] The combustion chamber is offset, and the offset δ is 4mm.
[0031] The arc necking radius ratio r / R of the upper and lower vortex chambers is 0.3.
[0032] There is a boundary ridge between the upper and lower vortex chambers, and the top fillet diameter of the boundary ridge is 4mm.
[0033] There is a diversion slope between the upper vortex chamber and the boundary ridge, and the diversion slope is tangent to the arc of the upper vortex chamber.
[0034] There is an upper vortex chamber top curved surface between the upper vortex chamber and the top of the piston, and the top end is a rounded corner with a diam...
specific Embodiment approach 2
[0037] Such as figure 1 Shown: a high and low double vortex chamber double constriction combustion chamber, the longitudinal section of the combustion chamber is butterfly-shaped, the combustion chamber is divided into two arc-shaped constriction vortex chambers distributed up and down, and the center of the combustion chamber is the arc top Round table.
[0038] The combustion chamber is offset, and the offset δ is 5mm.
[0039] The arc necking radius ratio r / R of the upper and lower vortex chambers is 1.3.
[0040] There is a boundary ridge between the upper and lower vortex chambers, and the diameter of the top fillet of the boundary ridge is 2 mm.
[0041] There is a diversion slope between the upper vortex chamber and the boundary ridge, and the diversion slope is tangent to the arc of the upper vortex chamber.
[0042] There is an upper vortex chamber top curved surface between the upper vortex chamber and the top of the piston, and the diameter of the top fillet is 2...
Embodiment approach 3
[0045] The difference from Embodiment 1 is that the arc constriction radius ratio r / R of the upper and lower vortex chambers is 0.7.
PUM
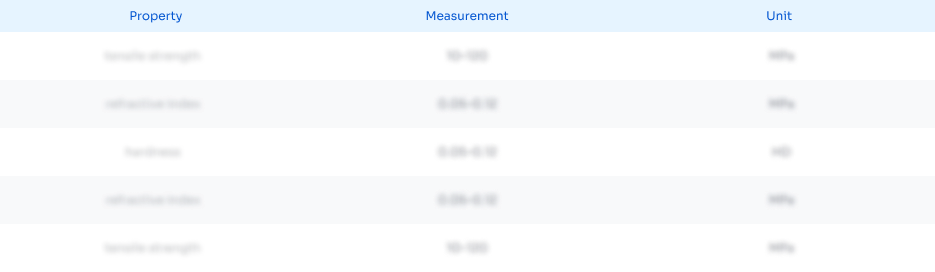
Abstract
Description
Claims
Application Information

- R&D
- Intellectual Property
- Life Sciences
- Materials
- Tech Scout
- Unparalleled Data Quality
- Higher Quality Content
- 60% Fewer Hallucinations
Browse by: Latest US Patents, China's latest patents, Technical Efficacy Thesaurus, Application Domain, Technology Topic, Popular Technical Reports.
© 2025 PatSnap. All rights reserved.Legal|Privacy policy|Modern Slavery Act Transparency Statement|Sitemap|About US| Contact US: help@patsnap.com