Automatic cable tie packaging equipment and automatic cable tie packaging method
A technology of automatic packaging and cable ties, which is applied in packaging, transportation packaging, packaging protection, etc., can solve the problems of low pass rate, low efficiency of manual bagging, and affecting sealing, so as to improve packaging quality and efficiency and facilitate large-scale The effect of improving production and production efficiency
- Summary
- Abstract
- Description
- Claims
- Application Information
AI Technical Summary
Problems solved by technology
Method used
Image
Examples
specific Embodiment approach
[0163] It should be noted that, referring to figure 1 As shown, the "X" axis direction involved in the present invention refers to the left-right direction, the "Y" axis direction refers to the front-rear direction, and the "Z" axis direction refers to the up-down vertical direction.
[0164] Wherein, "substantially horizontal" refers to a slight inclination, and the range of the inclination angle may be within 15°. In addition, the packaging container is also placed on the conveyor belt horizontally or substantially horizontally.
[0165] The structure of the existing semi-finished product is basically: the semi-finished product 500 includes a connecting strip 510, a plurality of cable tie finished products 520 perpendicular to it are connected to the two sides of the connecting strip 510, and a positioning opening 511 is opened on the connecting strip 510, and a connecting 510 Both ends are provided with connecting teeth 512 .
Embodiment 1
[0167] A kind of cable tie automatic packaging equipment, such as Figure 1~25 shown, including:
[0168] The material preparation device 100 includes a feeding mechanism 110, a material cutting mechanism 120 for cutting the semi-finished product 500 to obtain a finished product 520, a finished product receiving mechanism 130 for receiving the finished product, and a waste material receiving mechanism 140 for receiving the cut connecting strip;
[0169] The material shifting device 200 includes a material receiving mechanism 210 for receiving finished products in the finished product receiving mechanism 130, a material pushing mechanism 220 for moving finished products in the material receiving mechanism 210; a material cutting mechanism 120, a finished product receiving mechanism 130, and a material receiving mechanism 210 Set in order from top to bottom;
[0170]Packaging device 300, the present embodiment adopts packaging bag to carry out packaging, specifically comprises ...
Embodiment 2
[0262] The difference between it and Embodiment 1 is that there is a difference in the way of controlling the material cutting mechanism to start cutting, and the start of the material cutting mechanism can be controlled without calculating the feeding stroke.
[0263] Specifically, as Figure 26 Schematically, at the intersection of the feeding stroke and the cutting stroke, a pre-cut sensor 124 connected to the material preparation control module for collecting pre-cut signals is provided.
[0264] When the sliding part drives the semi-finished product 500 to move in the feeding stroke and approach the pre-cutting sensor 124, the pre-cutting sensor 124 collects the pre-cutting signal and sends it to the material preparation control module, and the material preparation control module receives the pre-cutting signal and controls the material cutting mechanism to start cutting. When the sliding part drives the semi-finished product to complete the cutting stroke, the material p...
PUM
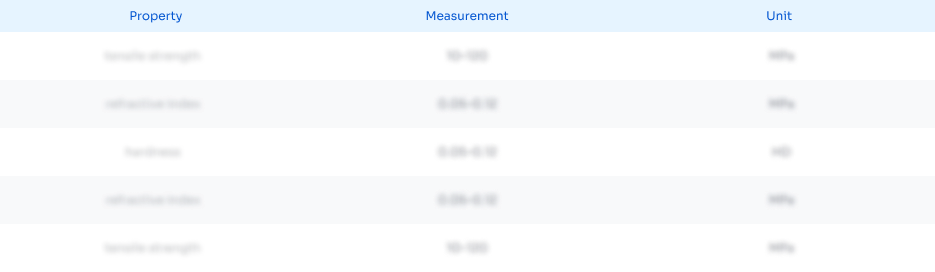
Abstract
Description
Claims
Application Information

- R&D Engineer
- R&D Manager
- IP Professional
- Industry Leading Data Capabilities
- Powerful AI technology
- Patent DNA Extraction
Browse by: Latest US Patents, China's latest patents, Technical Efficacy Thesaurus, Application Domain, Technology Topic, Popular Technical Reports.
© 2024 PatSnap. All rights reserved.Legal|Privacy policy|Modern Slavery Act Transparency Statement|Sitemap|About US| Contact US: help@patsnap.com