Preparation method of graphene modified polyester composite material based on liquid phase stripping
A polyester composite material and graphene modification technology, which is applied in the direction of graphene, chemical instruments and methods, carbon compounds, etc., can solve the problems of complex graphene preparation process, poor graphene integrity, and unfavorable performance. Stability and integrity, prevention of secondary agglomeration, high stability and integrity effects
- Summary
- Abstract
- Description
- Claims
- Application Information
AI Technical Summary
Problems solved by technology
Method used
Image
Examples
Embodiment 1
[0041] A method of graphene-modified polyester nanocomposite based on liquid phase exfoliation, comprising the following preparation steps:
[0042] 1) Take by weighing 7.68g expanded graphite and join in 396g ethylene glycol solution, then add 7.68g polyhydroxyglucose as dispersant, in ultrasonic cell breaker, ultrasonic 2h under the ultrasonic power of 1620W, obtain graphene dispersion liquid;
[0043] 2) Weigh 664g terephthalic acid, 0.172g titanium silica sol catalyst (titanium element content is 4ppm) and mix with graphene dispersion liquid, under pressure is 0.3Mpa, and temperature is 230 ℃ to carry out esterification reaction, until steamed The water reaches the theoretical value of 144g. Then, the temperature was raised to about 260° C., and the polycondensation reaction was carried out for 2.5 hours under a vacuum condition of 10 Pa to finally obtain a graphene polyester nanocomposite material.
Embodiment 2
[0045] 1) Take by weighing 3.84g expanded graphite and join in 372g ethylene glycol solution, then add 7.68g polyhydroxyglucose as dispersant, in ultrasonic cell breaker, ultrasonic 4h under the ultrasonic power of 1440W, obtain graphene dispersion liquid;
[0046] 2) Weigh 776g dimethyl terephthalate, 0.344g titanium silica sol catalyst (titanium element content is 8ppm) and mix with graphene dispersion liquid, carry out transesterification reaction at the temperature of 210 ℃, until the distilled methanol reaches The theoretical value is 256g. Then, the temperature was raised to about 265° C., and the polycondensation reaction was carried out for 2.7 hours under a vacuum condition of 20 Pa to finally obtain a graphene polyester nanocomposite material.
[0047] The difference with Example 1 is that Example 2 is a DMT transesterification method, while Example 1 is a PTA direct esterification method. Example 1 is easier to industrialize, and has no methanol generation, and the ...
Embodiment 3
[0049] 1) Take by weighing 0.768g expanded graphite and join in 372g ethylene glycol solution, then add 7.68g quinic acid as dispersant, in ultrasonic cell breaker, ultrasonic 2h under the ultrasonic power of 1080W, obtain graphene dispersion liquid;
[0050] 2) Weigh 776g of dimethyl terephthalate, 0.192g of ethylene glycol antimony catalyst and mix them with the graphene dispersion, and carry out transesterification reaction at a temperature of 170°C until the distilled methanol reaches a theoretical value of 256g. Then, the temperature was raised to about 270° C., and the polycondensation reaction was carried out for 2.5 hours under a vacuum condition of 20 Pa to finally obtain a graphene polyester nanocomposite material.
PUM
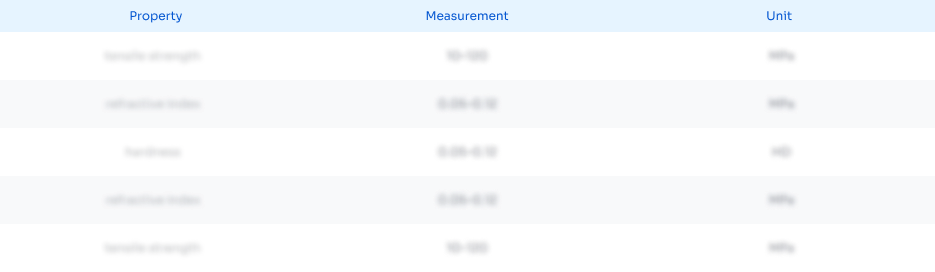
Abstract
Description
Claims
Application Information

- R&D
- Intellectual Property
- Life Sciences
- Materials
- Tech Scout
- Unparalleled Data Quality
- Higher Quality Content
- 60% Fewer Hallucinations
Browse by: Latest US Patents, China's latest patents, Technical Efficacy Thesaurus, Application Domain, Technology Topic, Popular Technical Reports.
© 2025 PatSnap. All rights reserved.Legal|Privacy policy|Modern Slavery Act Transparency Statement|Sitemap|About US| Contact US: help@patsnap.com