Substrate polishing system
A substrate and grinding layer technology, which is applied to grinding devices, grinding machine tools, and parts of grinding machine tools, can solve problems such as the inability to grasp the grinding layer of the substrate in real time, and the inability to accurately measure the thickness of the grinding layer in real time.
- Summary
- Abstract
- Description
- Claims
- Application Information
AI Technical Summary
Problems solved by technology
Method used
Image
Examples
Embodiment Construction
[0038] The present invention will be described in detail below with reference to the accompanying drawings. In describing the present invention, in order to clarify the gist of the present invention, detailed descriptions of well-known functions or configurations are omitted.
[0039] As shown in the figure, the substrate polishing system 1 of an embodiment of the present invention is used to flatly polish the polishing layer of the substrate W, comprising: a polishing disk 10, which is covered with a polishing pad 11 and rotates 11d; a slurry supply part (not shown) As shown in the figure), it supplies the slurry on the polishing pad 11; the polishing head 20, in the polishing process, pressurizes the substrate W so that the substrate W is located on the lower side; the regulator 40, which rotates 40d in the polishing process And the polishing pad 11 is pressurized and reformed; the slurry supply part (not shown), which supplies slurry to the polishing pad for the chemical fo...
PUM
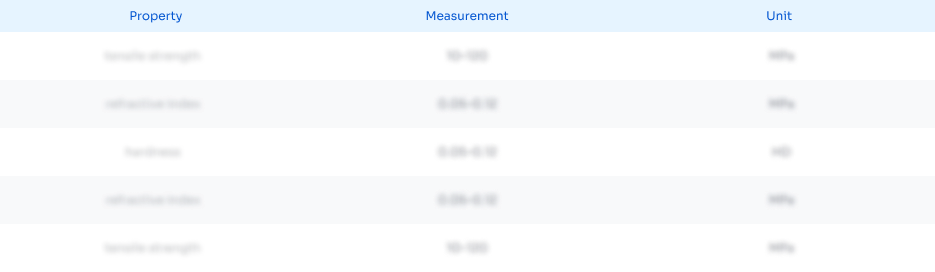
Abstract
Description
Claims
Application Information

- R&D Engineer
- R&D Manager
- IP Professional
- Industry Leading Data Capabilities
- Powerful AI technology
- Patent DNA Extraction
Browse by: Latest US Patents, China's latest patents, Technical Efficacy Thesaurus, Application Domain, Technology Topic, Popular Technical Reports.
© 2024 PatSnap. All rights reserved.Legal|Privacy policy|Modern Slavery Act Transparency Statement|Sitemap|About US| Contact US: help@patsnap.com