Single-component regenerated geopolymer cement concrete
A technology of cement concrete and geopolymer, applied in the field of concrete, can solve the problems of low utilization rate, dust pollution, and low resource value of parts with a particle size less than 5mm, and achieve the promotion of hydration and micro-aggregate effect, improvement of activity, The effect of improving resource utilization
- Summary
- Abstract
- Description
- Claims
- Application Information
AI Technical Summary
Problems solved by technology
Method used
Examples
Embodiment 1
[0021] Note: The amount of alkali activator is calculated according to the mass ratio of the precursor, which is: pozzolanic mineral admixture and regenerated sand / powder mixture;
[0022] Slag, recycled sand / powder mixture, Na 2 SiO 3 After weighing according to the mass ratio of 6.5:3.5:1.3, the slag and the regenerated sand / powder mixture are first ball milled at high speed for 2 hours, and then Na 2 SiO 3 Ball milling for half an hour to prepare single-component recycled geopolymer cement.
[0023] Stir and mix 1 part of single-component recycled geopolymer cement, 0.6 parts of recycled sand / powder mixture, 1.4 parts of standard sand, 0.35 parts of water, and 0.015 parts of water reducing agent to make a test block of 50mm×50mm×50mm. After curing for 1 day under the conditions of humidity above 95% and ambient temperature of 20±2°C, the formwork is removed and placed in water at a temperature of 20±2°C for curing. The strength of the curing age reaches 75.6Mpa after 28...
Embodiment 2
[0025] Fly ash, recycled sand / powder mixture, CaO, Na 2 SiO 3 After weighing according to the mass ratio of 6.5:3.5:0.5:0.8, the fly ash and the regenerated sand / powder mixture are first ball milled at high speed for 2 hours, and then CaO and Na 2 SiO 3 Ball milling for half an hour to prepare single-component recycled geopolymer cement.
[0026] Stir and mix 1 part of single-component recycled geopolymer cement, 0.6 parts of recycled sand / powder mixture, 1.4 parts of standard sand, 0.35 parts of water, and 0.015 parts of water reducing agent to make a test block of 50mm×50mm×50mm. After curing for 1 day under the conditions of humidity above 95% and ambient temperature of 20±2°C, the formwork was removed and placed in water at a temperature of 20±2°C for curing. The strength of the curing age reached 65.3Mpa after 28 days of curing.
Embodiment 3
[0028] Fly ash, slag, recycled sand / powder mixture, Na 2 SiO 3 and Na 2 CO 3 After weighing according to the mass ratio of 4:4.5:1.5:1:0.8, the mixture of fly ash, slag and recycled sand / powder will be ball-milled at high speed for 2 hours, and then the alkali activator Na 2 SiO 3 and Na 2 CO 3 Ball milling for half an hour to prepare single-component recycled geopolymer cement.
[0029] Stir and mix 1 part of single-component recycled geopolymer cement, 1 part of recycled sand / powder mixture, 1 part of standard sand, 0.35 part of water, and 0.02 part of water reducer to make a test block of 50mm×50mm×50mm, in the relative After curing for 1 day under the conditions of humidity above 95% and ambient temperature of 20±2°C, the formwork was removed and placed in water at a temperature of 20±2°C for curing. The strength of the curing age reached 63.9Mpa after 28 days of curing.
PUM
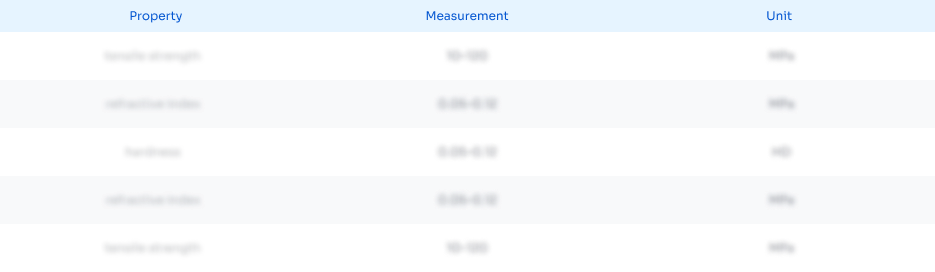
Abstract
Description
Claims
Application Information

- R&D
- Intellectual Property
- Life Sciences
- Materials
- Tech Scout
- Unparalleled Data Quality
- Higher Quality Content
- 60% Fewer Hallucinations
Browse by: Latest US Patents, China's latest patents, Technical Efficacy Thesaurus, Application Domain, Technology Topic, Popular Technical Reports.
© 2025 PatSnap. All rights reserved.Legal|Privacy policy|Modern Slavery Act Transparency Statement|Sitemap|About US| Contact US: help@patsnap.com