Permanent magnet brushless motor, robot joint, servo steering engine actuator and robot
A technology of permanent magnet brushless motors and permanent magnets, which is applied in servo servo actuators, permanent magnet brushless motors and robot joints, and in the field of robotics, and can solve limitations, low cogging torque, motor stability, and limited motor stator slots Full rate and other issues, to achieve the effect of increasing the slot full rate, increasing the motor constant and output power density, and meeting the design requirements
- Summary
- Abstract
- Description
- Claims
- Application Information
AI Technical Summary
Problems solved by technology
Method used
Image
Examples
Embodiment Construction
[0044] The following will clearly and completely describe the technical solutions in the embodiments of the present invention with reference to the accompanying drawings in the embodiments of the present invention. Obviously, the described embodiments are only some, not all, embodiments of the present invention. Based on the embodiments of the present invention, all other embodiments obtained by persons of ordinary skill in the art without making creative efforts belong to the protection scope of the present invention.
[0045] In order to enable those skilled in the art to better understand the solution of the present invention, the present invention will be further described in detail below in conjunction with the accompanying drawings and specific embodiments.
[0046] Such as Figure 1 to Figure 7 As shown, the embodiment of the present invention provides a permanent magnet brushless motor, which is a fractional slot inner rotor motor. The motor includes: a stator 1 and a...
PUM
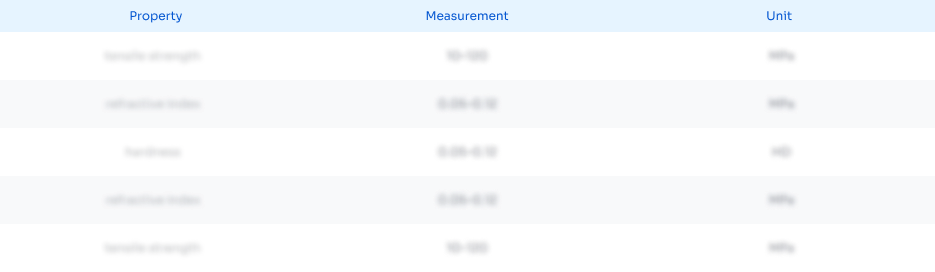
Abstract
Description
Claims
Application Information

- R&D
- Intellectual Property
- Life Sciences
- Materials
- Tech Scout
- Unparalleled Data Quality
- Higher Quality Content
- 60% Fewer Hallucinations
Browse by: Latest US Patents, China's latest patents, Technical Efficacy Thesaurus, Application Domain, Technology Topic, Popular Technical Reports.
© 2025 PatSnap. All rights reserved.Legal|Privacy policy|Modern Slavery Act Transparency Statement|Sitemap|About US| Contact US: help@patsnap.com