Woven bag coating, preparation method, coating method and woven bag
A woven bag and coating technology, which is applied in textiles and papermaking, textile/flexible product manufacturing, final product manufacturing, etc., can solve the problems of moisture, perforation, dust leakage, etc., and achieve dust reduction, strength retention, and tensile strength The effect of zero loss
- Summary
- Abstract
- Description
- Claims
- Application Information
AI Technical Summary
Problems solved by technology
Method used
Image
Examples
Embodiment 1
[0064] 1.1 Preparation of woven bag coating:
[0065] A woven bag coating provided by the present invention, its raw materials include: low-density polyethylene 7.5%; special-grade polypropylene 47%; first-grade polypropylene 38%; whitening agent: 0.4%; masterbatch: 6% ; Antireflection Masterbatch: 0.35%; Degradant: 0.08%; Paraffin: 0.67%.
[0066] 1.2 Preparation method:
[0067] (1) prepare each raw material by proportioning;
[0068] ① Preparation of super polypropylene;
[0069] The preparation method of the super-grade polypropylene is: mixing the drawing-grade polypropylene particles and the first-grade recycled polypropylene particles in a weight ratio of 2:8; then granulating the finished product, the ash content of which is 5%;
[0070] ② Preparation of primary polypropylene;
[0071] The preparation method of the primary polypropylene is: mixing the primary recycled polypropylene particles and the secondary recycled polypropylene particles in a weight ratio of 5:...
Embodiment 2
[0077] To prepare woven bag coating:
[0078] A woven bag paint provided by the present invention, its raw materials include: low-density polyethylene 15%; special-grade polypropylene 40%; first-grade polypropylene 31.2%; whitening agent: 0.3%; masterbatch: 10% ; Anti-reflection masterbatch: 2%; Cooling masterbatch: 0.5%; Paraffin wax: 1%.
[0079] Preparation:
[0080] (1) prepare each raw material by proportioning;
[0081] ① Preparation of super polypropylene;
[0082] The preparation method of the super-grade polypropylene is: mixing the drawing-grade polypropylene particles and the first-grade recycled polypropylene particles in a weight ratio of 1.5:8.5; then granulating the finished product, the ash content of which is 6%;
[0083] ② Preparation of primary polypropylene;
[0084] The preparation method of the primary polypropylene is: mixing the primary recycled polypropylene particles and the secondary recycled polypropylene particles in a weight ratio of 4:6; then...
Embodiment 3
[0090] To prepare woven bag coating:
[0091] A woven bag coating provided by the present invention, its raw materials include: 2% low-density polyethylene; 55.25% special-grade polypropylene; 30% first-grade polypropylene; whitening agent: 0.5%; masterbatch: 2% ; Anti-reflection masterbatch: 10%; Cooling masterbatch: 0.2%; Paraffin wax: 0.05%.
[0092] Preparation:
[0093] (1) prepare each raw material by proportioning;
[0094] ① Preparation of super polypropylene;
[0095] The preparation method of the super-grade polypropylene is: mixing the drawing-grade polypropylene particles and the first-grade recycled polypropylene particles in a weight ratio of 2.5:7.5; then granulating the finished product, the ash content of which is 4%;
[0096] ② Preparation of primary polypropylene;
[0097] The preparation method of the primary polypropylene is: mixing the primary recycled polypropylene particles and the secondary recycled polypropylene particles in a weight ratio of 6:4;...
PUM
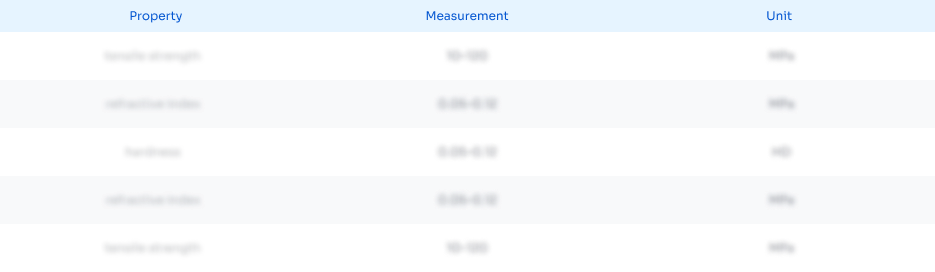
Abstract
Description
Claims
Application Information

- R&D
- Intellectual Property
- Life Sciences
- Materials
- Tech Scout
- Unparalleled Data Quality
- Higher Quality Content
- 60% Fewer Hallucinations
Browse by: Latest US Patents, China's latest patents, Technical Efficacy Thesaurus, Application Domain, Technology Topic, Popular Technical Reports.
© 2025 PatSnap. All rights reserved.Legal|Privacy policy|Modern Slavery Act Transparency Statement|Sitemap|About US| Contact US: help@patsnap.com