Reaction process for preparing 1, 3-butadiene by oxidizing and dehydrogenating 1-butene with carbon dioxide
A carbon dioxide, oxidative dehydrogenation technology, applied in carbon compound catalysts, catalysts, organic chemistry, etc., can solve the problems of low 1,3-butadiene selectivity, catalyst carbon deposition, poor stability, etc., to improve the resistance to carbon deposition. performance, extended life, and improved stability
- Summary
- Abstract
- Description
- Claims
- Application Information
AI Technical Summary
Problems solved by technology
Method used
Image
Examples
Embodiment 1
[0030] The oxidative dehydrogenation catalyst was prepared according to Example 22 in the patent CN201711157473.2.
[0031] Reaction evaluation process and conditions: The oxidative dehydrogenation reaction is carried out in a quartz tube fixed-bed reactor with an inner diameter of 7.6 mm, where the reaction pressure is normal pressure, the reaction temperature is 600 ° C, and the mass space velocity based on 1-butene is 4.5 grams 1-butene / g catalyst·hour, the molar ratio of 1-butene to carbon dioxide is 1:9, water is the diluent, the ratio of water to ene (water / 1-butene) is 5.0 (molar ratio), and the amount of catalyst is 0.2 g .
[0032] The results of the oxidative dehydrogenation reaction performance of Example 1 and the carbon deposition of the catalyst after the reaction are shown in Table 1.
Embodiment 2~5
[0034] Under the reaction conditions of Example 1, the catalyst in Example 1 was used to investigate the water-ene ratio in the carbon dioxide oxidation 1-butene dehydrogenation process conditions, so as to obtain the best water-ene ratio. Set the ratio of water to ene to 8.0, 9.0, 10.0, 11.0 respectively. The conversion rate of 1-butene, CO 2 The conversion rate, the selectivity of 1-butene to 1,3-butadiene, the space-time yield of 1,3-butadiene and the carbon deposition of the catalyst after 1 hour of reaction are used as indicators, and the obtained results are shown in Table 1.
[0035] It can be concluded from the results that after the introduction of water vapor, the space-time yield of 1,3-butadiene of the catalyst decreases, and it presents a "volcanic" distribution with the increase of the water-ene ratio, and when the water-ene ratio is 10.0 Extreme values appeared, in which the conversion rate of 1-butene was 76%, the selectivity of 1-butene to 1,3-butadiene was...
Embodiment 6~7
[0039] Under the reaction conditions of Example 4, the catalyst in Example 1 was used to investigate the reaction temperature in the carbon dioxide oxidation of 1-butene dehydrogenation process conditions, in order to explore the best reaction temperature. Set the reaction temperature as 500°C and 550°C respectively. The conversion rate of 1-butene, CO 2 The conversion rate, the selectivity of 1-butene to 1,3-butadiene and the space-time yield of 1,3-butadiene are indicators, and the obtained reaction performance results are shown in Table 2. It can be seen from Table 2 that the activity of the catalyst is not as high as that at 600°C when the reaction temperature is 500°C or 550°C. Therefore, 600°C is the optimal temperature for the reaction.
[0040] Table 2 Catalysis of CO by catalysts at different reaction temperatures 2 Reaction result of oxidative dehydrogenation of 1-butene
[0041]
PUM
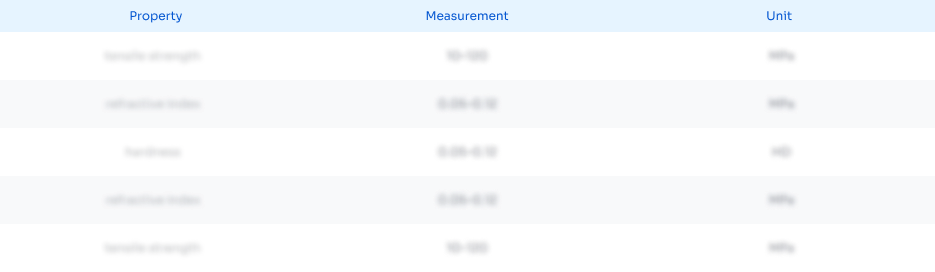
Abstract
Description
Claims
Application Information

- R&D
- Intellectual Property
- Life Sciences
- Materials
- Tech Scout
- Unparalleled Data Quality
- Higher Quality Content
- 60% Fewer Hallucinations
Browse by: Latest US Patents, China's latest patents, Technical Efficacy Thesaurus, Application Domain, Technology Topic, Popular Technical Reports.
© 2025 PatSnap. All rights reserved.Legal|Privacy policy|Modern Slavery Act Transparency Statement|Sitemap|About US| Contact US: help@patsnap.com