Degradable magnesium alloy in-situ composite anastomotic nail and preparation method thereof
An in-situ composite and anastomotic nail technology, applied in the direction of nails, mechanical equipment, metal material coating technology, etc., can solve the problems of fast degradation rate, low mechanical strength, poor plasticity, etc., to promote the growth and protection of bones and teeth Nervous system, strengthening and plasticity-enhancing effects
- Summary
- Abstract
- Description
- Claims
- Application Information
AI Technical Summary
Problems solved by technology
Method used
Image
Examples
Embodiment 1
[0032] In this example, the preparation method of anastomotic nails: by weight percentage, pure magnesium, 1% Zn, 1% Nd are smelted into liquid metal, cast into ingots, surface defects and impurities are removed, and homogenized heat treatment is performed at 400 ° C for 4 hours , Magnesium alloy rods with a diameter of 10mm are processed by hot extrusion at 430°C (the extrusion ratio is 70:1), and wires with a diameter of 0.3mm are drawn by cold drawing, and heat treatment and annealing are performed at 300°C for 60min. The magnesium alloy wire is prepared into a U-shaped staple, the bending part of the U-shaped staple is elliptical, the total length of the staple is 10-15 mm, the height of the staple is 3-6 mm, and the diameter of the end surface of the staple is 0.20-0.35 mm. Staples are electrolytically polished to remove surface defects and impurities. The polishing liquid adopts a volume ratio of ethylene glycol ether: dehydrated alcohol: a mixed solution of phosphoric ac...
Embodiment 2
[0035] In this example, the preparation method of anastomotic nails: by weight percentage, pure magnesium, 1.73% Zn, 0.68% Nd are smelted into liquid metal, cast into ingots, surface defects and impurities are removed, and homogenization heat treatment is performed at 380°C for 6 hours , Magnesium alloy rods with a diameter of 10mm are processed by hot extrusion at 420°C (the extrusion ratio is 60:1), and wires with a diameter of 0.3mm are drawn by cold drawing, and heat treatment and annealing are performed at 280°C for 120min. The magnesium alloy wire is prepared into a U-shaped staple, the bending part of the U-shaped staple is elliptical, the total length of the staple is 10-15 mm, the height of the staple is 3-6 mm, and the diameter of the end surface of the staple is 0.20-0.35 mm. Staples are electrolytically polished to remove surface defects and impurities. The polishing liquid adopts a volume ratio of ethylene glycol ether: dehydrated alcohol: phosphoric acid=1:2:2 mix...
Embodiment 3
[0038] In this example, the preparation method of anastomotic nails: by weight percentage, pure magnesium, 1.6% Zn, 0.7% Nd are smelted into liquid metal, cast into ingots, surface defects and impurities are removed, and homogenized heat treatment is performed at 420°C for 5 hours , Magnesium alloy rods with a diameter of 10mm are processed by hot extrusion at 410°C (the extrusion ratio is 80:1), and wires with a diameter of 0.3mm are drawn by cold drawing, and heat treatment and annealing are performed at 320°C for 30min. The magnesium alloy wire is prepared into a U-shaped staple, the bending part of the U-shaped staple is elliptical, the total length of the staple is 10-15 mm, the height of the staple is 3-6 mm, and the diameter of the end surface of the staple is 0.20-0.35 mm. Staples are electrolytically polished to remove surface defects and impurities. The polishing liquid adopts a volume ratio of ethylene glycol ether: dehydrated alcohol: a mixed solution of phosphoric ...
PUM
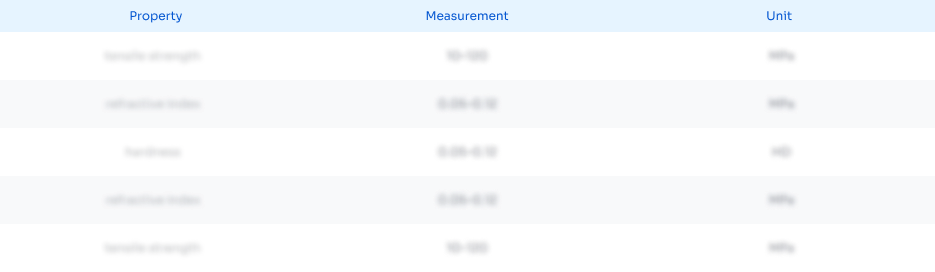
Abstract
Description
Claims
Application Information

- R&D Engineer
- R&D Manager
- IP Professional
- Industry Leading Data Capabilities
- Powerful AI technology
- Patent DNA Extraction
Browse by: Latest US Patents, China's latest patents, Technical Efficacy Thesaurus, Application Domain, Technology Topic, Popular Technical Reports.
© 2024 PatSnap. All rights reserved.Legal|Privacy policy|Modern Slavery Act Transparency Statement|Sitemap|About US| Contact US: help@patsnap.com