Unpowered non-force self-flat-pressing oil groove integrated flotation seal device
A floating seal, oil pressure tank technology, applied in the direction of hydropower, engine components, machines/engines, etc., can solve the problems of high labor intensity, long construction period, large workload, etc., and achieve simple and convenient dismantling and installation, long replacement time, The effect of short replacement time
- Summary
- Abstract
- Description
- Claims
- Application Information
AI Technical Summary
Problems solved by technology
Method used
Image
Examples
Embodiment Construction
[0025]A stop ring 11 is processed on the inner diameter side of the upper ring surface 10 and the lower ring surface 19 of the split seat ring 40 with the seat ring flange 27 and the joint surface 41, and the air inlet hole is processed on the vertical ring surface 9. 38, on the lower ring surface 19 of the outer side of the vertical ring surface 9, a flat pressure through hole 30 is processed, and the upper integrated rectangular groove ring 12 is formed by the upper ring 14 of the moment groove, the lower ring 34 of the moment groove and the fixing hole 37. Groove upper ring 14, the moment groove lower ring 34 with a plurality of oil injection holes 39 and the fixing hole 37 have formed the lower integrated rectangular groove ring 36, and each group has 4~16 pieces of backs that are fixed with pretension springs 13, with The split floating sealing body 16 of the positioning waist hole 33 is respectively placed in the upper integrated rectangular groove 12 and the lower integr...
PUM
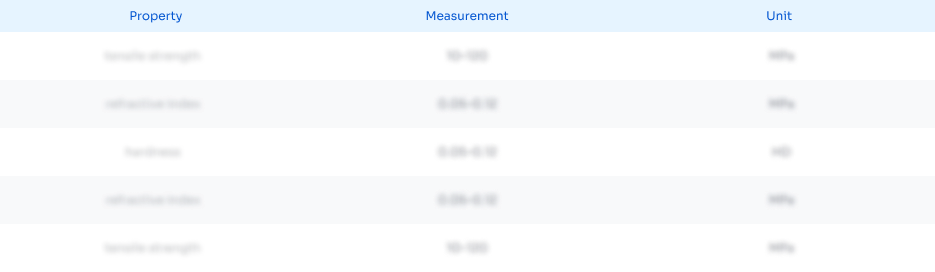
Abstract
Description
Claims
Application Information

- R&D
- Intellectual Property
- Life Sciences
- Materials
- Tech Scout
- Unparalleled Data Quality
- Higher Quality Content
- 60% Fewer Hallucinations
Browse by: Latest US Patents, China's latest patents, Technical Efficacy Thesaurus, Application Domain, Technology Topic, Popular Technical Reports.
© 2025 PatSnap. All rights reserved.Legal|Privacy policy|Modern Slavery Act Transparency Statement|Sitemap|About US| Contact US: help@patsnap.com