Paper product container processing method
A processing method and technology of paper products, applied in the fields of metal processing, textiles and papermaking, etc., can solve the problems of irrationality, long distribution of production lines, and low processing efficiency of paper products
- Summary
- Abstract
- Description
- Claims
- Application Information
AI Technical Summary
Problems solved by technology
Method used
Image
Examples
Embodiment 1
[0118] Such as figure 1 with figure 2 Shown, this a kind of paper product container processing method comprises the steps:
[0119] a1. Slurry forming, using Slurry Forming Machine 01 to perform Slurry Slurry, the slurry after Slurry Slurry is then subjected to primary extrusion heating molding and secondary extrusion heating molding through the Slurry Slurry Forming Machine to obtain paper Product container blanks;
[0120] The heating of the extrusion belt can not only shorten the subsequent hot press molding time, but also facilitate the transfer of the blank.
[0121] Further, the temperature of the primary extrusion thermoforming is lower than the temperature of the secondary extrusion thermoforming.
[0122] The temperature difference and the gradual increase design can preheat the wet billet and heat it after preheating to ensure product quality.
[0123] The number of suction pulp forming machine 01 can be set according to the actual production capacity, for examp...
Embodiment 2
[0268] The structure and principle of this embodiment are the same as that of Embodiment 1, the difference is that: the suction pulp forming machine, the mechanical transfer device and the trimming machine are located on the same straight line, and the total number of the hot presses is 1-8 Taiwan, and the hot press is distributed on either side of the same straight-line suction pulp forming machine and / or mechanical transfer device.
Embodiment 3
[0270] The structure and principle of this embodiment are the same as those of Embodiment 1, the difference lies in:
[0271] Such as Figure 14 Shown, wet base transfer mold C1 comprises base plate-C11, is provided with 1-12 vacuum-pumping hole-C12 on base plate-C11, is provided with wet base form C13 at the side of base plate-C11 away from product transfer mold C2, in wet The side of the base mold C13 near the base plate C11 is provided with an air chamber C14 equal in number to the vacuum hole C12 and one air chamber C14 communicates with a vacuum hole C12, on the side of the wet blank mold C13 away from the base plate C11 The above-mentioned wet billet adsorption pockets C10 are provided. The number of wet billet adsorption pockets C10 is equal to the number of air chambers C14, and each wet billet adsorption recess C10 communicates with an air chamber C14 through several air-permeable small holes C15.
PUM
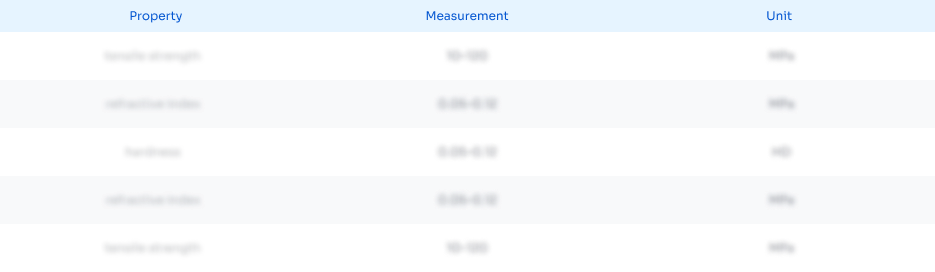
Abstract
Description
Claims
Application Information

- R&D Engineer
- R&D Manager
- IP Professional
- Industry Leading Data Capabilities
- Powerful AI technology
- Patent DNA Extraction
Browse by: Latest US Patents, China's latest patents, Technical Efficacy Thesaurus, Application Domain, Technology Topic, Popular Technical Reports.
© 2024 PatSnap. All rights reserved.Legal|Privacy policy|Modern Slavery Act Transparency Statement|Sitemap|About US| Contact US: help@patsnap.com