High-temperature liquid slag waste heat recovery system
A waste heat recovery system and liquid slag technology, applied in the direction of recycling technology, etc., can solve the problems of no waste heat recovery, large cooling water consumption, high pressure steam polluting the surrounding environment, etc., and achieve the effect of reducing the consumption and improving the utilization rate of waste heat.
- Summary
- Abstract
- Description
- Claims
- Application Information
AI Technical Summary
Problems solved by technology
Method used
Image
Examples
Embodiment 1
[0059] A waste heat recovery system for high-temperature liquid slag in this embodiment includes three parts: a slag receiving unit 100, a molten slag quick cooling unit 200, and a recovery unit 300, wherein the slag receiving unit 100 is used to receive high-temperature liquid slag, while the slag receiving unit 100 also transports the high-temperature liquid slag to the slag rapid cooling unit 200 under a certain pressure; It refers to giving the high-temperature liquid slag an instantaneous impact force, causing it to disperse into small liquid droplets, fall into the cooling water 241 and solidify into an amorphous glass phase to be discharged. pressure; at the same time, the recovery unit 300 exchanges heat with soft water for the mixed steam in the slag quick cooling unit 200, and the clean steam formed by the heat exchange is recycled, that is, heat energy is converted into electric energy.
[0060] Concrete combination figure 1 Specifically, the slag receiving unit 10...
Embodiment 2
[0067] This embodiment is basically the same as Embodiment 1, except that the deflector 220 forms an included angle of 80° with the inner wall of the molten slag quick-cooling high-pressure tank 210, and the swirl nozzle 140 beats the high-temperature liquid slag at a pressure of 500Kpa. On the deflector 220; at the same time, the slag rapid cooling unit 200 also includes a pressure gauge 231 and a pressure relief valve 232, that is, a pressure gauge 231 and a pressure relief valve 232 are installed above the slag rapid cooling high-pressure tank 210, and the slag rapid cooling The pressure in the high pressure tank 210 should be kept within a stable range of 480kPa. During normal operation of the system, if the pressure in the tank is higher than the value range, it will be monitored by the pressure gauge 231, and the pressure reducing valve 232 should be adjusted accordingly to reach the normal range, such as figure 2 Shown; Correspondingly, the pressure of high pressure wat...
Embodiment 3
[0069]The inventor tried to change the angle of the deflector 220 and the output pressure of the high-temperature pump 120 to study the particle size of the solidified amorphous glass phase in the slag quick-cooling high-pressure tank 210, and wanted to obtain as much solid slag as possible, so as to make full use of the high-temperature liquid slag energy, reduce the post-treatment process of solid slag, and make it easy to recycle to the cement plant for use. It is found that the high-temperature liquid slag reaches the position of the deflector 220 (the angle between the deflector 220 and the vertical direction is between 20-80°C), when the pressure of the high-temperature pump 120 is too high, the angle between the deflector 220 and the vertical direction If the included angle is too small, high-temperature slag will splash on the side wall of the slag quick-cooling high-pressure tank 210. After a long time, too much liquid slag will accumulate on the side wall, wear the sl...
PUM
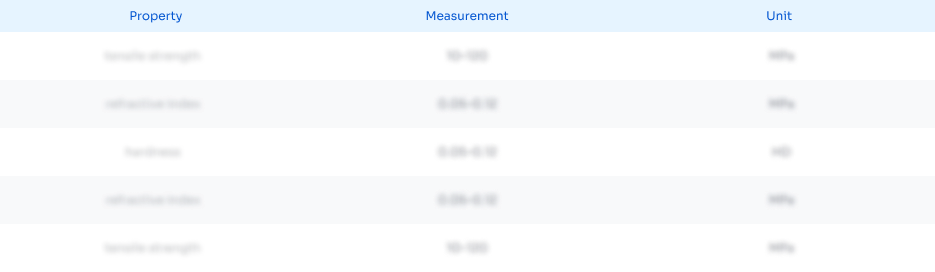
Abstract
Description
Claims
Application Information

- R&D Engineer
- R&D Manager
- IP Professional
- Industry Leading Data Capabilities
- Powerful AI technology
- Patent DNA Extraction
Browse by: Latest US Patents, China's latest patents, Technical Efficacy Thesaurus, Application Domain, Technology Topic, Popular Technical Reports.
© 2024 PatSnap. All rights reserved.Legal|Privacy policy|Modern Slavery Act Transparency Statement|Sitemap|About US| Contact US: help@patsnap.com