Padding device for producing textile
A textile and padding technology, which is applied in the field of textile production, can solve the problems of recycling and waste of dyeing liquid, impossibility of fabric padding, and inability to accurately control the force of pressing rollers, etc.
- Summary
- Abstract
- Description
- Claims
- Application Information
AI Technical Summary
Problems solved by technology
Method used
Image
Examples
Embodiment 1
[0029] as attached Figure 1-4 The shown padding equipment for textile production includes a pad dyeing pool 1, and the left and right sides of the pad dyeing pool 1 are respectively provided with a feed inlet 2, a discharge port 3, and ends of the feed port 2 and the discharge port 3. The cloth inlet wheel 4 and the cloth outlet wheel 5 which are located inside the pad dyeing pool 1 are fixedly installed on the upper part, and the dipping roller 6 and the pad dyeing stick 9 are installed in rotation inside the pad dyeing pool 1, and the bottom end of the discharge port 3 is fixedly installed. There is a partition 13, the inner side of the partition 13 and the pad dyeing pool 1 form a closed cavity, the outer side of the partition 13 is provided with a power chamber 14, and the outer side of the partition 13 is fixedly installed with a transmission box 16 located inside the power chamber 14, The output end of the transmission box 16 is fixedly connected with the stirring shaft...
Embodiment 2
[0039] The difference with the above-mentioned embodiment is embodied in: the appended Figure 5 Shown: includes a pad dyeing pool 1, the left and right sides of the pad dyeing pool 1 are respectively provided with a feed port 2 and a discharge port 3, and the ends of the feed port 2 and the discharge port 3 are fixedly installed with The cloth inlet wheel 4 and the cloth outlet wheel 5 located inside the pad dyeing pool 1 are equipped with dipping rollers 6 and pad dyeing sticks 9 rotating inside the pad dyeing pool 1, and the bottom end of the discharge port 3 is fixedly installed with Partition 13, the inner side of the partition 13 and the pad dyeing pool 1 form a closed cavity, the outside of the partition 13 is provided with a power chamber 14, and the outside of the partition 13 is fixedly installed with a The transmission box 16, the output end of the transmission box 16 is fixedly connected with the stirring shaft 8 located inside the pad dyeing pool 1, and one end of ...
PUM
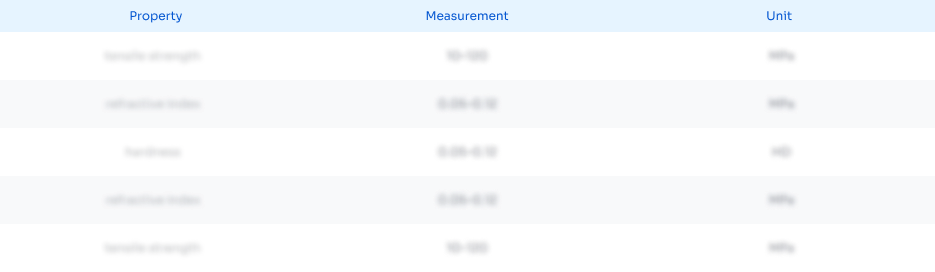
Abstract
Description
Claims
Application Information

- R&D Engineer
- R&D Manager
- IP Professional
- Industry Leading Data Capabilities
- Powerful AI technology
- Patent DNA Extraction
Browse by: Latest US Patents, China's latest patents, Technical Efficacy Thesaurus, Application Domain, Technology Topic, Popular Technical Reports.
© 2024 PatSnap. All rights reserved.Legal|Privacy policy|Modern Slavery Act Transparency Statement|Sitemap|About US| Contact US: help@patsnap.com