Process and device for producing glycine by alcohol phase method
A production process, glycine technology, applied in chemical instruments and methods, preparation of organic compounds, organic chemistry, etc., can solve the problems of high production cost, high equipment and pipeline requirements, high equipment operation and maintenance costs, and achieve production cost reduction , significant economic benefits, and significant environmental benefits
- Summary
- Abstract
- Description
- Claims
- Application Information
AI Technical Summary
Problems solved by technology
Method used
Image
Examples
Embodiment 1
[0031]A device for producing glycine by the alcohol phase method, 4 inlets of the chloroacetic acid dissolving kettle are connected to the methanol pipeline, the bottom valve of the chloroacetic acid dissolving kettle 4 is connected to the mixed crystal synthesis kettle 1; the inlet of the mixed crystal synthesis kettle 1 is connected with the ammonia gas pipeline, the vacuum pipeline and the mother liquor Pipeline, mixed crystal synthesis kettle 1 clamping socket connected to circulating water pipeline, mixed crystal synthesis kettle bottom valve connected to centrifuge; centrifuge 5 inlet connected to mixed crystal pipeline, methanol pipeline, nitrogen pipeline, extraction liquid pipeline, mother liquor discharge port of centrifuge The mother liquor receiving tank 6 and the dilute methanol tank 8; the bottom valve pipeline of the mother liquor receiving tank 6 is connected with the mother liquor jacket tank 3 through the mother liquor pump; the dilute methanol tank 8 is connec...
Embodiment 2
[0033] In a K2000L chloroacetic acid dissolution kettle, dissolve 1000kg solid chloroacetic acid (95.7%) with 1000L methanol and stir well. Dissolve 400kg of urotropine in a K8000L mixed crystal synthesis kettle with 2000L of methanol, stir well, and raise the temperature to 45°C. Pass ammonia gas into the mixed crystal synthesis kettle at 200kg / h, and drop the methanol solution of chloroacetic acid into the mixed crystal synthesis kettle at 600L / h at the same time, measure the pH once every 15min, maintain pH=7.5 in the whole reaction process, pass the mixing The coil and jacket in the crystal synthesis kettle control the temperature in the kettle to 50°C, and the total amount of ammonia passing through is about 340kg. When the methanol solution of chloroacetic acid is added dropwise, the heat preservation timer starts, and the heat preservation time is 4h. The synthetic liquid in the mixed crystal synthesis kettle is centrifuged out of the mixed crystal by centrifugation, a...
Embodiment 3
[0037] In a K2000L chloroacetic acid dissolution kettle, dissolve 1000kg of solid chloroacetic acid (95.1%) with 1000L methanol and stir thoroughly. Dissolve 300kg of urotropine in a K8000L mixed crystal synthesis kettle with 2000L of methanol, stir well, and raise the temperature to 45°C. Pass ammonia gas into the mixed crystal synthesis kettle at 200kg / h, and drop the methanol solution of chloroacetic acid into the mixed crystal synthesis kettle at 600L / h at the same time, measure the pH once every 15min, maintain pH=7.5 in the whole reaction process, pass the mixing The coil and jacket in the crystal synthesis kettle control the temperature in the kettle to 60°C, and the total amount of ammonia passing through is about 340kg. When the methanol solution of chloroacetic acid is added dropwise, the heat preservation timer starts, and the heat preservation time is 3h. The synthetic liquid in the mixed crystal synthesis kettle is centrifuged out of the mixed crystal by centrifu...
PUM
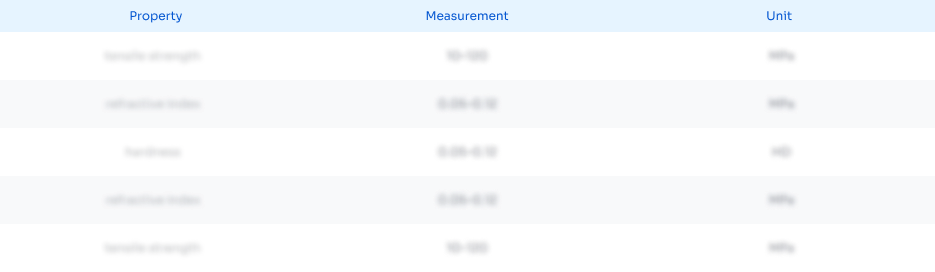
Abstract
Description
Claims
Application Information

- Generate Ideas
- Intellectual Property
- Life Sciences
- Materials
- Tech Scout
- Unparalleled Data Quality
- Higher Quality Content
- 60% Fewer Hallucinations
Browse by: Latest US Patents, China's latest patents, Technical Efficacy Thesaurus, Application Domain, Technology Topic, Popular Technical Reports.
© 2025 PatSnap. All rights reserved.Legal|Privacy policy|Modern Slavery Act Transparency Statement|Sitemap|About US| Contact US: help@patsnap.com