A rotor oil-cooled permanent magnet motor
A permanent magnet motor, oil cooling technology, applied in electromechanical devices, electrical components, electric components, etc., can solve the problems of poor cooling effect of permanent magnet rotor, high noise of permanent magnet motor, complex structure, etc., to increase the complexity, heat pipe The effect of short structural path and increased volumetric weight
- Summary
- Abstract
- Description
- Claims
- Application Information
AI Technical Summary
Problems solved by technology
Method used
Image
Examples
Embodiment 1
[0019] figure 1 , figure 2 Shown is a basic embodiment of the rotor oil-cooled permanent magnet motor based on the flow channel structure of the present invention. The motor consists of a stator assembly 3, a permanent magnet rotor 1 and sliding bearings on the left and right sides. The stator part is a conventional AC motor stator, and the inner rotor is a radial surface-mounted permanent magnet pole type. The permanent magnet rotor 1 includes a rotating shaft 1.1 and a rotor bracket. 1.3. The rotor yoke 1.4 and the permanent magnet pole 1.5. The driving end is equipped with a first sliding bearing 2 with thrust, and the non-driving end is equipped with a second sliding bearing 4 that only supports radially. The center hole of the rotating shaft 1.1 is filled with lubricating oil The axial flow passage of the shaft needs to be blocked according to the specific structure. The driving end of the shaft 1.1 is provided with two shaft shoulders 1.2. In order to minimize the infl...
Embodiment 2
[0029] Figure 5 Shown is a basic embodiment of the rotor oil-cooled permanent magnet motor based on the heat pipe structure of the present invention. The difference between this embodiment and Embodiment 1 lies in the pole segments of the permanent magnets of the rotor.
[0030] In this embodiment, the rotor bracket 1.3 and the rotor yoke 1.4 are respectively provided with heat pipes 1.6. The heat pipes 1.6 are connected to each other and extend to the central flow channel. The heat pipe 1.6 collects the heat of the permanent magnet pole 1.5 and transfers it to the central flow channel. The lubricating oil is taken away; the lubricating oil flow path of the heat pipe structure is short, and the lubricating oil flows in the center of the rotating shaft, which is suitable for higher speeds and has a lower demand for lubricating oil pressure.
[0031] The rotating shaft 1.1 of this embodiment can firstly process the blind hole in the center from the non-driving end, and then se...
PUM
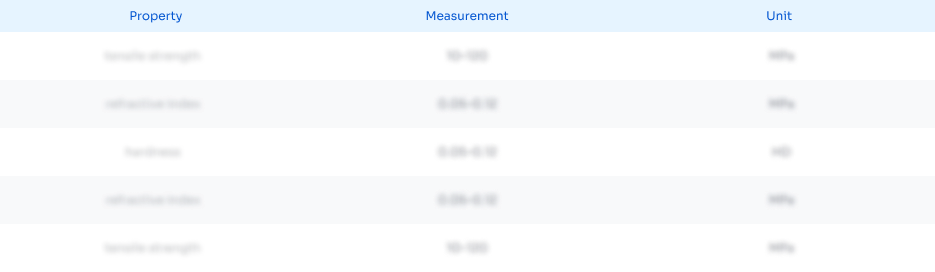
Abstract
Description
Claims
Application Information

- R&D Engineer
- R&D Manager
- IP Professional
- Industry Leading Data Capabilities
- Powerful AI technology
- Patent DNA Extraction
Browse by: Latest US Patents, China's latest patents, Technical Efficacy Thesaurus, Application Domain, Technology Topic, Popular Technical Reports.
© 2024 PatSnap. All rights reserved.Legal|Privacy policy|Modern Slavery Act Transparency Statement|Sitemap|About US| Contact US: help@patsnap.com