Discharging structure of plastic extruder
A plastic extruder and extruder technology, applied in the field of plastic processing, can solve the problem of different sizes of plastic particles, achieve basically the same size, and improve the effect of production quality
- Summary
- Abstract
- Description
- Claims
- Application Information
AI Technical Summary
Problems solved by technology
Method used
Image
Examples
Embodiment Construction
[0019] The following will clearly and completely describe the technical solutions in the embodiments of the present invention with reference to the accompanying drawings in the embodiments of the present invention. Obviously, the described embodiments are only some, not all, embodiments of the present invention.
[0020] refer to Figure 1-3 , a discharge structure of a plastic extruder, comprising a base 1, an extruder 2 and a screening box 3 are respectively fixedly installed on the top of the base 1, a discharge pipe 4 is arranged on the extruder 2, and the bottom of the discharge pipe 4 The end extends into the screening box 3, the inner wall of the screening box 3 is rotatably connected with a rotating ring 5, and the rotating ring 5 is slidably connected with a conical screen 6, and the bottom inner wall of the screening box 3 is fixedly installed with a driving motor 10 and a protective screen respectively. cover, and the driving motor 10 is located in the protective co...
PUM
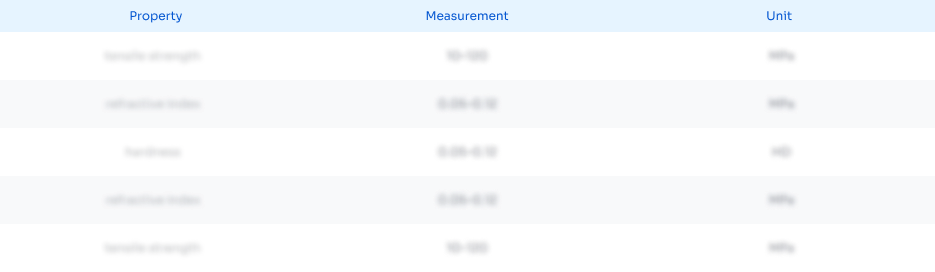
Abstract
Description
Claims
Application Information

- R&D
- Intellectual Property
- Life Sciences
- Materials
- Tech Scout
- Unparalleled Data Quality
- Higher Quality Content
- 60% Fewer Hallucinations
Browse by: Latest US Patents, China's latest patents, Technical Efficacy Thesaurus, Application Domain, Technology Topic, Popular Technical Reports.
© 2025 PatSnap. All rights reserved.Legal|Privacy policy|Modern Slavery Act Transparency Statement|Sitemap|About US| Contact US: help@patsnap.com