Gravity compensator with low rigidity and large suspension force
A technology of gravity compensation and levitation force, which is applied in the direction of magnetic attraction or thrust holding device, electrical components, etc., can solve the problems of high levitation stiffness and low levitation force of magnetic levitation gravity compensator, and achieve low levitation stiffness and large levitation force , the effect of increasing the magnetic field strength
- Summary
- Abstract
- Description
- Claims
- Application Information
AI Technical Summary
Problems solved by technology
Method used
Image
Examples
Embodiment 1
[0033] Such as Figure 1-Figure 8 As shown: this embodiment provides a gravity compensator with low stiffness and large levitation force, including a stator part and a mover part, and the stator part includes a stator fixing structure, a permanent magnet in the inner ring of the stator, a coil 7 and a permanent magnet in the outer ring of the stator , the stator inner ring permanent magnet, the coil 7 and the stator outer ring permanent magnet are all fixed on the stator fixed structure, the mover part includes the mover fixed structure, the mover inner ring permanent magnet 17 and the mover outer ring permanent magnet 16, the mover Both the permanent magnets 17 of the inner ring and the permanent magnets 16 of the outer ring of the mover are fixed on the fixed structure of the mover. The permanent magnets 17 of the inner ring of the mover are arranged on the inner side of the permanent magnets 16 of the outer ring of the mover. The permanent magnet 17, the coil 7, the permane...
Embodiment 2
[0055] The difference between this embodiment and Embodiment 1 is that the first stator inner ring permanent magnet 10 and the first stator outer ring permanent magnet 3 are magnetized by radiation from outside to inside, and the third stator inner ring permanent magnet 12 and the third stator inner ring permanent magnet 12 are magnetized from outside to inside. The permanent magnets 5 of the stator outer ring are all radiated and magnetized from the inside to the outside, the magnetization direction of the second stator inner ring permanent magnet 11 is from top to bottom, and the magnetization direction of the second stator outer ring permanent magnet 4 is from bottom to top, Both the permanent magnets 17 of the inner ring of the mover and the permanent magnets 16 of the outer ring of the mover are magnetized radially from outside to inside, and the equivalent magnetization direction of the coil 7 is from top to bottom.
PUM
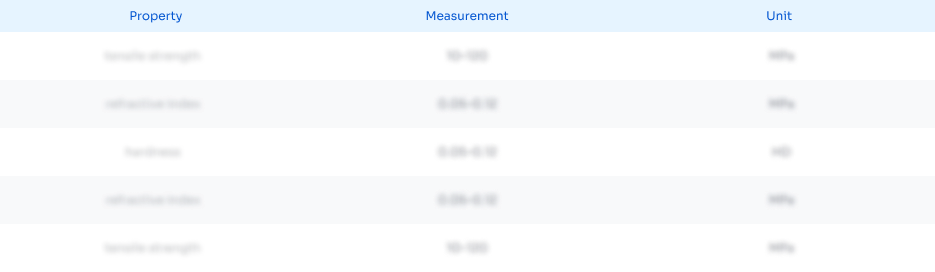
Abstract
Description
Claims
Application Information

- Generate Ideas
- Intellectual Property
- Life Sciences
- Materials
- Tech Scout
- Unparalleled Data Quality
- Higher Quality Content
- 60% Fewer Hallucinations
Browse by: Latest US Patents, China's latest patents, Technical Efficacy Thesaurus, Application Domain, Technology Topic, Popular Technical Reports.
© 2025 PatSnap. All rights reserved.Legal|Privacy policy|Modern Slavery Act Transparency Statement|Sitemap|About US| Contact US: help@patsnap.com