PCB, layout method and device thereof and storage medium
A PCB board, prohibiting wiring technology, applied in the field of PCB board design, can solve the problems of increasing PCB cost, unfavorable product miniaturization, etc., and achieve the effect of increasing current carrying capacity, reliable design principle, and saving wiring area
- Summary
- Abstract
- Description
- Claims
- Application Information
AI Technical Summary
Problems solved by technology
Method used
Image
Examples
Embodiment 1
[0034] Such as figure 1 and 2 As shown, the present embodiment provides a PCB board, including:
[0035] The PCB board body is provided with an inner layer power supply layer in the PCB board body, a top layer power supply layer is provided on the top layer of the PCB board body, and copper sheets are provided on both the inner layer power supply layer and the top layer power supply layer; There are milling slot holes, and a tin layer is plated in the milling slot holes. The bottom end of the tin layer is connected to the inner layer power layer, and the top end of the tin layer is connected to the top layer power layer. The signal layer is isolated from the tin layer.
Embodiment 2
[0037] Such as figure 1 and 2 As shown, a method for laying out a PCB board provided in this embodiment includes the following steps:
[0038] S1: In the bottleneck area of the power transmission plane, along the current transmission direction, lay a copper sheet with a width of at least 0.5mm on the surface of the PCB; then lay a window area and a steel mesh area on the surface copper sheet; center on the surface copper sheet Set the silk screen label; lay a forbidden wiring area on the adjacent layer between the second outer layer and the power layer; the width of the window area is 0.4mm; the width of the steel mesh area is 0.5mm; the silk screen label width is 0.2mm; the wiring area is prohibited The width is 0.5mm.
[0039] S2: During PCB processing, use a milling cutter to mill grooves in the area marked by silk screen. The depth of the milling grooves only drills through the low-voltage and high-current power layer, and does not touch the next layer of the power pla...
Embodiment 3
[0043] Embodiment 3: This embodiment provides a layout device for PCB boards, including:
[0044] PCB surface layer laying module,
[0045] In the bottleneck area of the power transmission plane, along the current transmission direction, lay a copper sheet with a width of at least 0.5mm on the surface of the PCB; then lay out the window area and the steel mesh area on the surface copper sheet; set the silk screen around the surface copper sheet Marking; Lay the forbidden wiring area on the adjacent layer between the second outer layer and the power layer;
[0046] slot milling module,
[0047] During PCB processing, use a milling cutter to mill the groove in the silk screen marked area. The depth of the milling groove only drills through the low-voltage and high-current power layer, and does not touch the next layer of the power plane;
[0048] tinned modules,
[0049] During PCB placement, the stencil area at the milling slot is partially thickened to increase the amount...
PUM
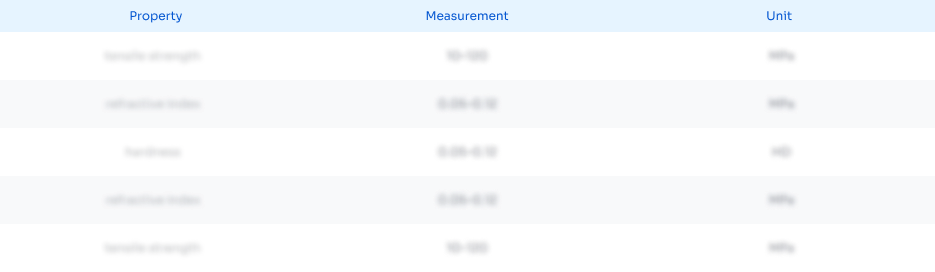
Abstract
Description
Claims
Application Information

- R&D
- Intellectual Property
- Life Sciences
- Materials
- Tech Scout
- Unparalleled Data Quality
- Higher Quality Content
- 60% Fewer Hallucinations
Browse by: Latest US Patents, China's latest patents, Technical Efficacy Thesaurus, Application Domain, Technology Topic, Popular Technical Reports.
© 2025 PatSnap. All rights reserved.Legal|Privacy policy|Modern Slavery Act Transparency Statement|Sitemap|About US| Contact US: help@patsnap.com