Sound-absorbing rigid polyurethane foam composite material for vehicles
A polyurethane rigid foam combination material and vehicle-use technology, applied in the field of polyurethane, can solve the problems of limited application range, poor foam mechanical properties, and low sound absorption coefficient
- Summary
- Abstract
- Description
- Claims
- Application Information
AI Technical Summary
Problems solved by technology
Method used
Image
Examples
Embodiment 1
[0037] Preparation of component A:
[0038] Accurately measure 58 parts of polyether polyol A (functionality 3, molecular weight 4700), 16 parts of polyester polyol (2 functionality, molecular weight 300), 15 parts of polyether polyol B (functionality 3, molecular weight 500) , 1.5 parts of chain extender ethylene glycol, 3 parts of diethylene glycol, catalyst tetramethyliminodipropylamine Jeffcat Z-130 (U.S. Huntsman Company) 0.3 parts, N, N, N'-trimethyl- N'-hydroxyethyl bisaminoethyl ether Jeffcat Z-10 (U.S. Huntsman company) 0.2 part, pentamethyldiethylenetriamine Polycat 5 (Evonik Industrial Group) 0.15 part, surfactant Tegostab B 8870 (win 0.85 parts of Evonik Industrial Group), 2 parts of Ortegol 501 (Evonik Industrial Group), and 3 parts of water were put into the reaction kettle, stirred and mixed for 2 hours, and sealed and packaged.
[0039] Component B: polymethylene polyphenyl polyisocyanate
[0040] The materials of components A and B are mixed and reacted acco...
Embodiment 2
[0042] Preparation of component A:
[0043] Accurately measure 60 parts of polyether polyol A (functionality 3, molecular weight 6000), 20 parts of polyester polyol (2 functionality, molecular weight 660), 10 parts of polyether polyol B (functionality 4, molecular weight 700) , chain extender glycerol 4.5 parts, catalyst N-methyl-N-(dimethylaminopropyl) aminoethanol Polycat 17 (Evonik Industrial Group) 0.5 parts, N, N-bis(dimethylaminopropyl) ) Isopropanolamine Jeffcat ZR-50 (U.S. Huntsman Company) 0.5 part, catalyst bis(2-dimethylaminoethyl) ether Polycat BL-17 (Evonik Industrial Group) 0.1 part, surfactant AK-8805 ( Jiangsu Meisid Chemical Co., Ltd.) 0.15 parts, surfactant AK-6680 (Jiangsu Meisid Chemical Co., Ltd.) 0.75 parts, surfactant AK-9905 (Jiangsu Meisid Chemical Co., Ltd.) 1.5 parts, Put 2 parts of water into the reaction kettle, stir and mix for 2 hours, take out the material after sampling and testing, and seal the package;
[0044] Component B: polymethylene po...
Embodiment 3
[0047] Preparation of component A:
[0048] Accurately measure 46 parts of polyether polyol A (functionality 3, molecular weight 3000), 23.5 parts of polyester polyol (2 functionality, molecular weight 2000), 18 parts of polyether polyol B (functionality 3, molecular weight 300) , 7 parts of chain extender dipropylene glycol, catalyst N, N-dimethylaminoethyl-N'-methylaminoethanol Jeffcat ZR-110 (U.S. Huntsman Company) 0.2 parts, 2,2-bismorpholino diethyl Base ether Dabco DMDEE (Evonik Industrial Group Company) 0.5 part, surfactant L-580 (Momentive) 0.7 part, Tegostab B 8523 (Evonik Industrial Group Company) 0.2 part, water 3.9 parts, put into the reaction kettle, stir and mix 2 hours, after sampling and testing, discharge and seal the package.
[0049] Component B: polymethylene polyphenyl polyisocyanate
[0050] The materials of components A and B are mixed and reacted according to the weight ratio of A:B=100:95 to prepare foam, and the quality of the product is tested.
PUM
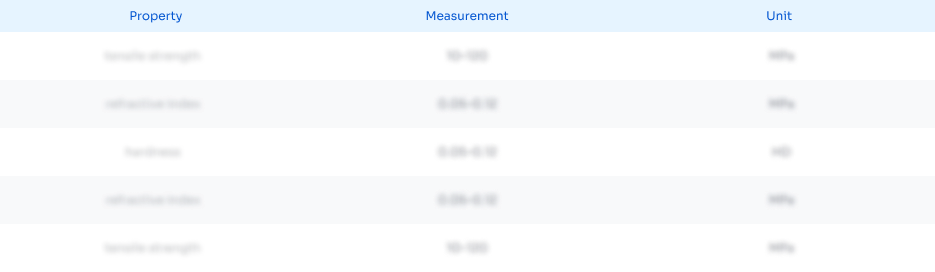
Abstract
Description
Claims
Application Information

- R&D
- Intellectual Property
- Life Sciences
- Materials
- Tech Scout
- Unparalleled Data Quality
- Higher Quality Content
- 60% Fewer Hallucinations
Browse by: Latest US Patents, China's latest patents, Technical Efficacy Thesaurus, Application Domain, Technology Topic, Popular Technical Reports.
© 2025 PatSnap. All rights reserved.Legal|Privacy policy|Modern Slavery Act Transparency Statement|Sitemap|About US| Contact US: help@patsnap.com