Liquid level online real-time monitoring system for quantitative casting of magnesium alloy
A real-time monitoring system, magnesium alloy technology, applied to the equipment for supplying molten metal, the configuration of indicating equipment/measuring equipment, casting equipment, etc., can solve the problems of inaccurate quantitative casting, inaccurate liquid level monitoring data, etc., and achieve product quality Reliable quality, high reliability, and the effect of reducing production costs
- Summary
- Abstract
- Description
- Claims
- Application Information
AI Technical Summary
Problems solved by technology
Method used
Image
Examples
Embodiment 1
[0029] Embodiment 1: A magnesium alloy melting furnace is selected as a melting furnace with a diameter of 1.5 m and a height of 1 m. The liquid inlet of the melt pump is fixed at a vertical distance of 20mm from the bottom of the furnace. During the smelting and casting process of the molten magnesium, the height of the molten magnesium is always controlled at 35-75mm. The protective gas is argon.
[0030] Input the volume of magnesium melt that needs to be poured into the control system as 0.22m 3 , the height of the liquid level before casting is 0.701m, and the PLC control system selects the appropriate melt pump rotor speed of 35Hz and rotation time of 9.7s according to the measured liquid level. The theoretical drop height should be 0.125m, the actual drop height is 0.125m, and the error is almost 0.
example 2
[0031] Example 2: The magnesium alloy melting furnace is selected as a melting furnace with a diameter of 1.5m and a height of 1m. The liquid inlet of the melt pump is fixed at a vertical distance of 20mm from the bottom of the furnace. During the smelting and casting process of the molten magnesium, the height of the molten magnesium is always controlled at 35-75mm. The protective gas is argon.
[0032] Input the volume of magnesium melt that needs to be poured into the control system as 0.22m 3 , the height of the liquid level before casting is 0.576m, and the PLC control system selects the appropriate melt pump rotor speed of 35Hz and rotation time of 11.2s according to the measured liquid level. The theoretical drop height should be 0.125m, the actual drop height is 0.126m, and the error is 0.8%.
example 3
[0033] Example 3: The magnesium alloy melting furnace is selected as a melting furnace with a diameter of 1.5m and a height of 1m. The liquid inlet of the melt pump is fixed at a vertical distance of 20mm from the bottom of the furnace. During the smelting and casting process of the molten magnesium, the height of the molten magnesium is always controlled at 35-75mm. The protective gas is argon.
[0034] Input the volume of magnesium melt that needs to be poured into the control system as 0.22m 3, the height of the liquid level before casting is 0.451m, and the PLC control system selects the appropriate melt pump rotor speed of 35Hz and rotation time of 13s according to the measured liquid level. The theoretical drop height should be 0.125m, the actual drop height is 0.125m, and the error is almost 0.
PUM
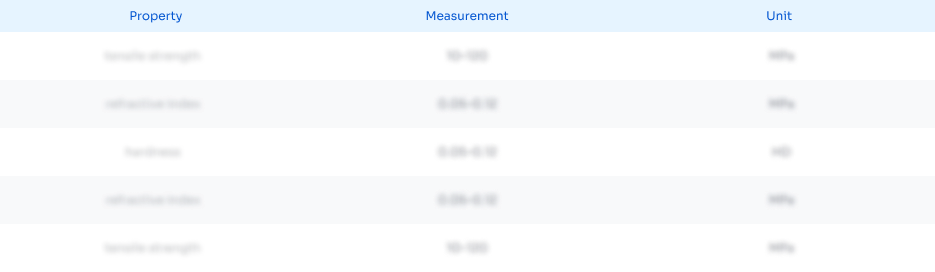
Abstract
Description
Claims
Application Information

- R&D
- Intellectual Property
- Life Sciences
- Materials
- Tech Scout
- Unparalleled Data Quality
- Higher Quality Content
- 60% Fewer Hallucinations
Browse by: Latest US Patents, China's latest patents, Technical Efficacy Thesaurus, Application Domain, Technology Topic, Popular Technical Reports.
© 2025 PatSnap. All rights reserved.Legal|Privacy policy|Modern Slavery Act Transparency Statement|Sitemap|About US| Contact US: help@patsnap.com