High-nitrogen low-oxygen silicon nitride vanadium iron alloy and preparation method thereof
A technology for silicon vanadium oxynitride ferroalloy and ferrosilicon vanadium oxynitride is applied in the field of high nitrogen and low oxygen silicon vanadium nitride ferroalloy and its preparation, and can solve the problems of many kinds of production raw materials, incapability of large-scale production and unstable nitrogen content and other problems, to achieve the effect of controllable component content, dense product, and high nitrogen content
- Summary
- Abstract
- Description
- Claims
- Application Information
AI Technical Summary
Problems solved by technology
Method used
Examples
preparation example Construction
[0031] The present invention also provides a method for preparing a high-nitrogen and low-oxygen silicon-vanadium-iron alloy, comprising the following steps:
[0032] Step 1: Grinding ferrosilicon vanadium into 100-400 mesh fine powder, in step 1, the amount of the binder added is 7-8% of the mixture quality, (the binder is industrial starch and water according to the weight The ratio of 1:4 is mixed and configured), stirred and mixed, and the mixture is pressed into a block with a press; wherein, the composition of the ferrosilicon vanadium is composed by weight percentage: vanadium 35%-40%, silicon 12% -18%, carbon≤0.5%, sulfur≤0.05%, phosphorus≤0.05%, and the balance is Fe.
[0033] Step 2: Put the pressed massive ferrosilicon vanadium into the electric drying kiln, and dry it under the condition of 300-400 ℃;
[0034] Step 3: Put the dried bulk ferrosilicon vanadium into the high vacuum sintering furnace, and then send electricity to raise the temperature under the condit...
Embodiment 1
[0040] A preparation method of high-nitrogen and low-oxygen silicon-vanadium-iron alloy, comprising the following steps:
[0041] Step 1: Grind ferrosilicon vanadium into 100 mesh fine powder, then add binding agent, the amount that described binding agent adds is 7% of mixture quality, (binding agent is industrial starch and water according to weight ratio 1: 4 ratio mixed configuration). Stir and mix evenly, and press the mixture into blocks with a press; wherein, the composition of the ferrosilicon vanadium is composed of 35% vanadium, 12% silicon, 0.5% carbon, 0.05% sulfur, 0.05% phosphorus, and the remaining The amount is Fe.
[0042] Step 2: Put the pressed massive ferrosilicon vanadium into the electric drying kiln, and dry it at 300°C;
[0043] Step 3: Put the dried bulk ferrosilicon vanadium into the high vacuum sintering furnace, and then send electricity to raise the temperature under the condition of vacuum degree of 0.01Pa. Nitriding of vanadium is carried out ...
Embodiment 2
[0046] A preparation method of high-nitrogen and low-oxygen silicon-vanadium-iron alloy, comprising the following steps:
[0047] Step 1: Grind ferrosilicon vanadium into 200 mesh fine powder with Raymond mill, then add binder, the amount of said binder added is 7.5% of the mass of the mixture, (the binder is industrial starch and water according to It is mixed and configured at a weight ratio of 1:4). Stir and mix evenly, and press the mixture into blocks with a press; wherein, the composition of the ferrosilicon vanadium is composed of 38% vanadium, 16% silicon, 0.3% carbon, 0.03% sulfur, 0.04% phosphorus, and the remaining The amount is Fe.
[0048] Step 2: Put the pressed massive ferrosilicon vanadium into the electric drying kiln, and dry it at 380°C;
[0049] Step 3: Put the dried bulk ferrosilicon vanadium into the high vacuum sintering furnace, and then send electricity to raise the temperature under the condition of vacuum degree of 0.8Pa. Nitriding of vanadium is ...
PUM
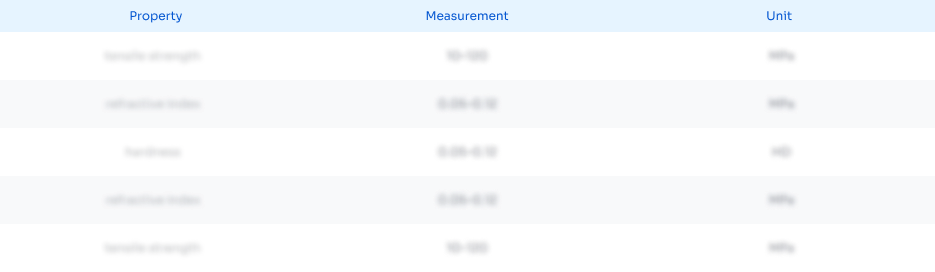
Abstract
Description
Claims
Application Information

- R&D
- Intellectual Property
- Life Sciences
- Materials
- Tech Scout
- Unparalleled Data Quality
- Higher Quality Content
- 60% Fewer Hallucinations
Browse by: Latest US Patents, China's latest patents, Technical Efficacy Thesaurus, Application Domain, Technology Topic, Popular Technical Reports.
© 2025 PatSnap. All rights reserved.Legal|Privacy policy|Modern Slavery Act Transparency Statement|Sitemap|About US| Contact US: help@patsnap.com