Accurate positioning method of tooling plate
A precise positioning and tooling board technology, applied in image data processing, instruments, calculations, etc., can solve the problem of poor positioning accuracy and cannot meet high-precision positioning requirements, and achieve the effect of improving positioning accuracy.
- Summary
- Abstract
- Description
- Claims
- Application Information
AI Technical Summary
Problems solved by technology
Method used
Image
Examples
Embodiment Construction
[0024] In order to make the object, technical solution and advantages of the present invention clearer, the present invention will be further described in detail below in conjunction with the accompanying drawings and specific embodiments. It should be understood that the specific embodiments described here are only used to explain the present invention, but not to limit the present invention.
[0025] In order to solve the problem that the poor positioning accuracy of the purely mechanical positioning method of the tooling plate cannot meet the high-precision positioning requirements, the invention adds non-contact machine vision positioning on the basis of pure mechanical positioning, and performs secondary positioning on the tooling plate, and the machine Visual positioning is a non-contact real-time measurement method, which can improve the positioning accuracy of the tooling plate, and is not affected by factors such as mechanical parts wear and tooling plate variables. Th...
PUM
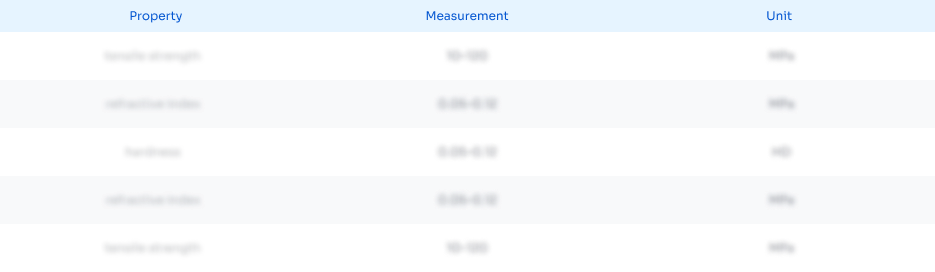
Abstract
Description
Claims
Application Information

- R&D
- Intellectual Property
- Life Sciences
- Materials
- Tech Scout
- Unparalleled Data Quality
- Higher Quality Content
- 60% Fewer Hallucinations
Browse by: Latest US Patents, China's latest patents, Technical Efficacy Thesaurus, Application Domain, Technology Topic, Popular Technical Reports.
© 2025 PatSnap. All rights reserved.Legal|Privacy policy|Modern Slavery Act Transparency Statement|Sitemap|About US| Contact US: help@patsnap.com