Aluminum alloy surface anodic oxidation coloring treatment production line and treatment process
An aluminum alloy surface, anodic oxidation technology, applied in the direction of anodic oxidation, surface reaction electrolytic coating, coating, etc., can solve the problems of waist fatigue, low processing efficiency, time-consuming and laborious handling, etc., to reduce the number of times of bending, The effect of reducing labor intensity and increasing success rate
- Summary
- Abstract
- Description
- Claims
- Application Information
AI Technical Summary
Problems solved by technology
Method used
Image
Examples
Embodiment Construction
[0026] The following will clearly and completely describe the technical solutions in the embodiments of the present invention with reference to the accompanying drawings in the embodiments of the present invention. Obviously, the described embodiments are only some, not all, embodiments of the present invention. Based on the embodiments of the present invention, all other embodiments obtained by persons of ordinary skill in the art without making creative efforts belong to the protection scope of the present invention.
[0027] see Figure 1-5 , the present invention provides the following technical solutions: aluminum alloy surface anodic oxidation and coloring treatment production line, comprising an oxidation room 1, the oxidation room 1 is provided with an oxidation tank 11, a coloring tank 12 and a closed tank 13 sequentially along the entrance side to the outlet side, the oxidation room 1 A cleaning tank 14 is provided on the outside of the exit side, and a transmission ...
PUM
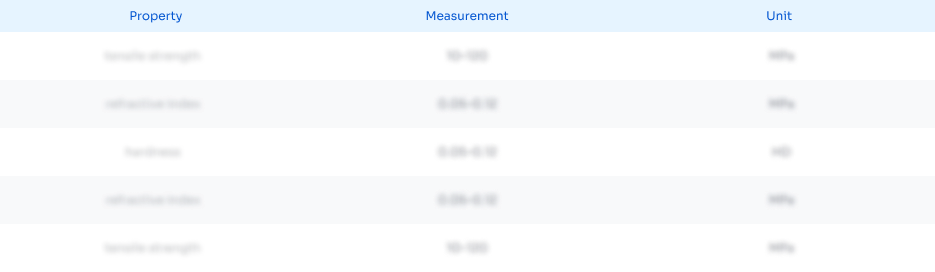
Abstract
Description
Claims
Application Information

- Generate Ideas
- Intellectual Property
- Life Sciences
- Materials
- Tech Scout
- Unparalleled Data Quality
- Higher Quality Content
- 60% Fewer Hallucinations
Browse by: Latest US Patents, China's latest patents, Technical Efficacy Thesaurus, Application Domain, Technology Topic, Popular Technical Reports.
© 2025 PatSnap. All rights reserved.Legal|Privacy policy|Modern Slavery Act Transparency Statement|Sitemap|About US| Contact US: help@patsnap.com