Tear-resistant sole material and manufacturing method thereof
A kind of sole material and tear-resistant technology, applied in the direction of sole, footwear, application, etc., can solve the problems of low tear resistance and easy cracking of the sole, and achieve the effect of good tear resistance
- Summary
- Abstract
- Description
- Claims
- Application Information
AI Technical Summary
Problems solved by technology
Method used
Image
Examples
Embodiment 1
[0045] A tear-resistant shoe sole material, comprising the following components by weight:
[0046] 60 parts of natural rubber 20STR;
[0047] EPDM4520 40 copies;
[0048] 5 parts of compatibilizer;
[0049] 45 parts of fillers, fillers include 35wt% light calcium carbonate, 50wt% white carbon black and 15wt% modified glass fibers;
[0050] Active zinc oxide 3.5 parts;
[0051] 1.8 parts of stearic acid;
[0052] 3 parts of foaming agent, foaming agent is foaming agent AC;
[0053] 2.8 parts of vulcanizing agent DCP, i.e. dicumyl peroxide;
[0054] Accelerator CZ 0.45 parts;
[0055] Anti-aging agent 0.3 parts, the anti-aging agent is compounded by anti-aging agent RD and anti-aging agent 4010 in equal mass ratio.
[0056] The preparation process of the compatibilizer is as follows: in parts by weight, first mix 11 parts of bromobutyl rubber and 0.25 parts of BPO, heat to 65°C, knead for 18 minutes, then add 0.6 parts of octadecyltrimethoxysilane, Raise the temperature...
Embodiment 2
[0064] A tear-resistant shoe sole material, comprising the following components by weight:
[0065] 55 parts of natural rubber 20STR;
[0066] EPDM4520 45 copies;
[0067] 4 parts of compatibilizer;
[0068] 40 parts of filler, filler includes 35wt% light calcium carbonate, 50wt% white carbon black and 15wt% modified glass fiber;
[0069] Active zinc oxide 3 parts;
[0070] 1.5 parts of stearic acid;
[0071] 2 parts of foaming agent, foaming agent is foaming agent AC;
[0072] 2.5 parts of vulcanizing agent DCP, i.e. dicumyl peroxide;
[0073] Accelerator CZ 0.3 parts;
[0074] Anti-aging agent 0.2 parts, the anti-aging agent is compounded by anti-aging agent RD and anti-aging agent 4010 in equal mass ratio.
[0075] The preparation process of the compatibilizer is as follows: in parts by weight, first mix 10 parts of bromobutyl rubber and 0.2 parts of BPO, heat to 60°C, knead for 15 minutes, then add 0.5 parts of octadecyltrimethoxysilane, Raise the temperature to 11...
Embodiment 3
[0083] A tear-resistant shoe sole material, comprising the following components by weight:
[0084] 65 parts of natural rubber 20STR;
[0085] EPDM4520 35 copies;
[0086] 6 parts of compatibilizer;
[0087] 50 parts of fillers, fillers include 35wt% light calcium carbonate, 50wt% white carbon black and 15wt% modified glass fibers;
[0088] Active zinc oxide 4 parts;
[0089] 2 parts stearic acid;
[0090] 4 parts of foaming agent, foaming agent is foaming agent AC;
[0091] 3 parts of vulcanizing agent DCP, namely dicumyl peroxide;
[0092] Accelerator CZ 0.6 parts;
[0093] Anti-aging agent 0.4 parts, the anti-aging agent is compounded by anti-aging agent RD and anti-aging agent 4010 in equal mass ratio.
[0094] The preparation process of the compatibilizer is as follows: in parts by weight, first mix 12 parts of bromobutyl rubber and 0.3 parts of BPO, heat to 70°C, knead for 20 minutes, then add 0.7 parts of octadecyltrimethoxysilane, Raise the temperature to 120°C...
PUM
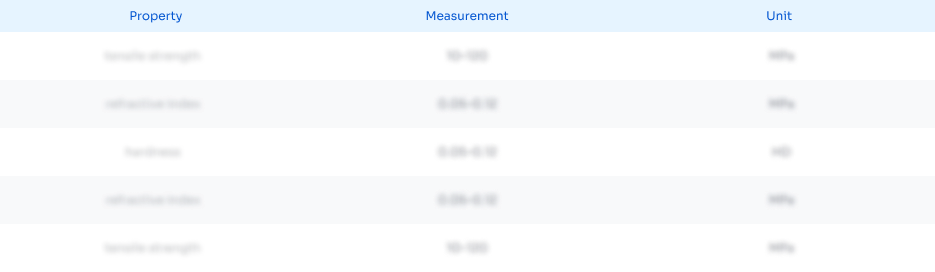
Abstract
Description
Claims
Application Information

- Generate Ideas
- Intellectual Property
- Life Sciences
- Materials
- Tech Scout
- Unparalleled Data Quality
- Higher Quality Content
- 60% Fewer Hallucinations
Browse by: Latest US Patents, China's latest patents, Technical Efficacy Thesaurus, Application Domain, Technology Topic, Popular Technical Reports.
© 2025 PatSnap. All rights reserved.Legal|Privacy policy|Modern Slavery Act Transparency Statement|Sitemap|About US| Contact US: help@patsnap.com