Emulsion preparation method based on steam explosion lignin
A lignin and steam explosion technology, which is applied in the field of emulsion preparation based on steam explosion lignin, can solve the problems of difficult separation and poor stability of emulsifiers, and achieve the effect of broadening the utilization channels
- Summary
- Abstract
- Description
- Claims
- Application Information
AI Technical Summary
Problems solved by technology
Method used
Examples
Embodiment 1
[0016] (1) Preparation of lignin from steam-exploded corn stalks: put 100 g of corn stalks into a steam explosion tank at 1.5 Mpa for 5 minutes, release the pressure quickly, and obtain steam-exploded wheat straw. The steam-exploded wheat straw was mixed with 1% NaOH at a ratio of 1:10 and maintained at 121 °C for 1 h, and the filtrate was obtained by filtering with 8 layers of gauze. The filtrate was precipitated with 3M hydrochloric acid, centrifuged and washed 3 times, and the steam-exploded corn stalk lignin was obtained.
[0017] (1) Preparation of steam-exploded corn stalk graft copolymer / cyclohexane emulsion: respectively add steam-exploded acid analysis of lignin and sodium lignosulfonate and 0.1mol / L NaOH solution into a three-necked flask (solid-to-liquid ratio 1: 50), the alkali breaks the ether bond of lignin to form more phenolic hydroxyl groups, thereby activating lignin. Then add a quantitative ratio of acrylamide monomer (40g / L), further stir under the protect...
Embodiment 2
[0021] (1) Preparation of steam-exploded wheat straw lignin: 100 g of wheat straw was put into a steam-exploded tank at 1.5 Mpa for 5 minutes, and the pressure was quickly released to obtain steam-exploded wheat straw. The steam-exploded wheat straw was mixed with 1% NaOH at a ratio of 1:10 and maintained at 121 °C for 1 h, and the filtrate was obtained by filtering with 8 layers of gauze. The filtrate was precipitated with 3M hydrochloric acid, centrifuged and washed three times to obtain steam-exploded wheat straw lignin.
[0022] (2) Preparation of steam-exploded wheat straw lignin graft copolymer / cyclohexane emulsion: respectively add steam-exploded acid analysis lignin and sodium lignosulfonate and 0.1mol / L NaOH solution into a three-neck flask (solid-liquid ratio 1:50), the alkali breaks the ether bond of lignin to form more phenolic hydroxyl groups, thereby activating lignin. Then add a quantitative ratio of acrylamide monomer (40g / L), further stir under nitrogen prote...
Embodiment 3
[0026] (1) Preparation of lignin from steam-exploded corn stalks: put 100 g of corn stalks into a steam explosion tank at 1.5 Mpa for 5 minutes, release the pressure quickly, and obtain steam-exploded wheat straw. The steam-exploded wheat straw was mixed with 1% NaOH at a ratio of 1:10 and maintained at 121 °C for 1 h, and the filtrate was obtained by filtering with 8 layers of gauze. The filtrate was precipitated with 3M hydrochloric acid, centrifuged and washed 3 times, and the steam-exploded corn stalk lignin was obtained.
[0027] (2) Preparation of steam-exploded corn stalk lignin graft copolymer / chloroform emulsion: add steam-exploded acid-analyzed lignin and sodium lignosulfonate and 0.1mol / L NaOH solution into a three-neck flask (solid-liquid ratio 1:50), the alkali breaks the ether bond of lignin to form more phenolic hydroxyl groups, thereby activating lignin. Then add a quantitative ratio of acrylamide monomer (40g / L), further stir under nitrogen protection to homo...
PUM
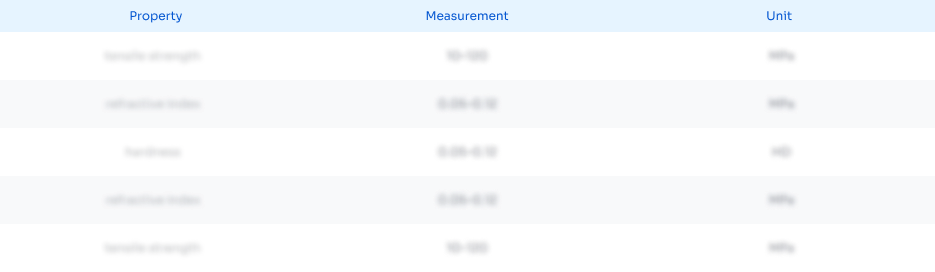
Abstract
Description
Claims
Application Information

- R&D Engineer
- R&D Manager
- IP Professional
- Industry Leading Data Capabilities
- Powerful AI technology
- Patent DNA Extraction
Browse by: Latest US Patents, China's latest patents, Technical Efficacy Thesaurus, Application Domain, Technology Topic, Popular Technical Reports.
© 2024 PatSnap. All rights reserved.Legal|Privacy policy|Modern Slavery Act Transparency Statement|Sitemap|About US| Contact US: help@patsnap.com