Assembling method of connecting rod and bearing shell of compressor
An assembly method and technology of connecting rod bearing bushes, which are applied in the direction of connecting rod bearings, metal processing, metal processing equipment, etc., can solve the problems of strength reduction, cumbersome processing, unfavorable production, etc., achieve long service life, reduce production costs, reduce The effect of maintenance times
- Summary
- Abstract
- Description
- Claims
- Application Information
AI Technical Summary
Problems solved by technology
Method used
Image
Examples
Embodiment Construction
[0017] The technical solutions of the present invention will be further specifically described below through embodiments and in conjunction with the accompanying drawings.
[0018] Such as figure 1 As shown, the present invention provides a method for assembling the connecting rod bearing shell of a compressor. 3 is installed in the small end of the connecting rod 1 through interference fit. After the connecting rod small end 2 and the bearing bush 3 are installed with an interference fit, they are installed with a clearance fit with the crosshead pin, and then assembled into the compressor and put into use.
[0019] The assembly method provided by the present invention includes the following steps: process the outer diameter of the bearing bush 3 with an interference of 0.08-0.12 mm, and then immerse it in liquid nitrogen to cool for 2-5 minutes. At this time, the mechanical properties of the bearing bush 3 remain unchanged, but the diameter can shrink by 0.4 About mm, take...
PUM
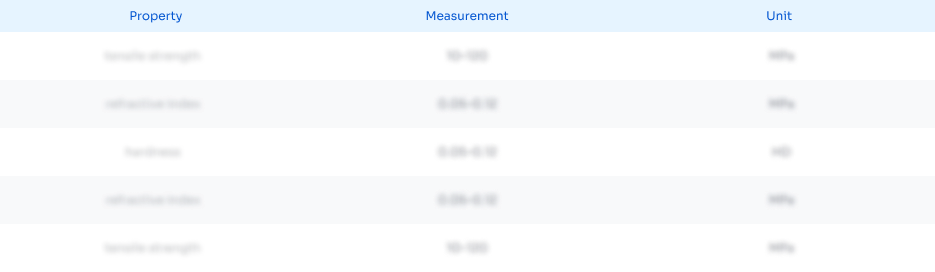
Abstract
Description
Claims
Application Information

- R&D
- Intellectual Property
- Life Sciences
- Materials
- Tech Scout
- Unparalleled Data Quality
- Higher Quality Content
- 60% Fewer Hallucinations
Browse by: Latest US Patents, China's latest patents, Technical Efficacy Thesaurus, Application Domain, Technology Topic, Popular Technical Reports.
© 2025 PatSnap. All rights reserved.Legal|Privacy policy|Modern Slavery Act Transparency Statement|Sitemap|About US| Contact US: help@patsnap.com