Optimal design method of aircraft inner flap mechanism
An optimization design and flap technology, applied in design optimization/simulation, geometric CAD, etc., can solve the problem of incapable of optimal design of flap mechanism, and achieve the effect of rational design optimization, loss reduction, and failure rate reduction.
- Summary
- Abstract
- Description
- Claims
- Application Information
AI Technical Summary
Problems solved by technology
Method used
Image
Examples
Embodiment approach
[0087] During the dynamic analysis of the flap lowering process, it was found that there are two main parameters that can reflect the stiffness and smoothness of the slide rail. One is the torsion angle caused by the deformation of the slide rail during the motion process. When the torsion angle increases, the influence of the roller The ability to move through the slide rail increases the movement resistance of the slide rail; another parameter is the stress. When the force between the slide rail and the roller increases, the stress on the slide rail will inevitably increase, which can also reflect The smoothness of the slide rail movement. On the other hand, whether the weight of aviation components can be improved during optimization is also an important aspect to measure whether the optimization goal can be achieved. Therefore, in the present disclosure, three example implementations are proposed, specifically as follows, example implementation 1: take the maximum stress a...
PUM
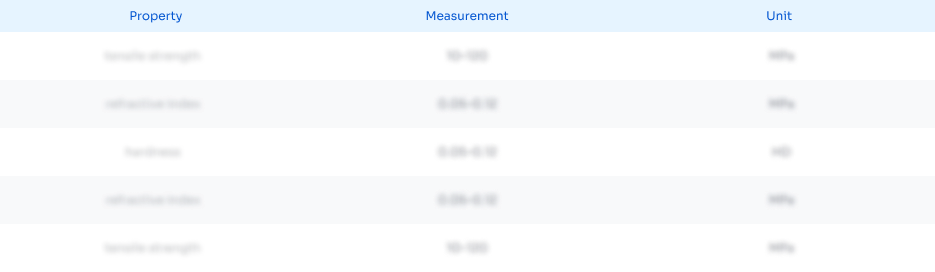
Abstract
Description
Claims
Application Information

- R&D
- Intellectual Property
- Life Sciences
- Materials
- Tech Scout
- Unparalleled Data Quality
- Higher Quality Content
- 60% Fewer Hallucinations
Browse by: Latest US Patents, China's latest patents, Technical Efficacy Thesaurus, Application Domain, Technology Topic, Popular Technical Reports.
© 2025 PatSnap. All rights reserved.Legal|Privacy policy|Modern Slavery Act Transparency Statement|Sitemap|About US| Contact US: help@patsnap.com