Thermocompression Forming Method of Fiber Reinforced Composite Wrinkled Sandwich Cone Shell
A fiber-reinforced and composite material technology, which is applied in the field of composite material molding design, can solve the problems such as the unprepared pleated sandwich circular frustum shell process, and achieve the effects of saving preparation time and cost, reducing production cost, and reducing cutting
- Summary
- Abstract
- Description
- Claims
- Application Information
AI Technical Summary
Problems solved by technology
Method used
Image
Examples
specific Embodiment approach 1
[0083] Specific implementation mode one: combine Figure 1 to Figure 25 Describe this embodiment, the hot press molding method of the fiber-reinforced composite material corrugated sandwich circular frustum shell of this embodiment,
[0084] Described method is realized through the following steps:
[0085] 1. Preparation of fiber-reinforced composite pleated core:
[0086] Step a, cleaning the core mold:
[0087] Clean the core mold with detergent and place it in a ventilated place to dry;
[0088] Step b, apply the release agent:
[0089] Spread the release agent evenly on the surface of the core mold, and then place it in a ventilated place until the core mold is completely dry;
[0090] Step c, assemble the core mold:
[0091] Assemble the first male mold 1-1 and the second male mold 1-2 in the core mold into a complete cone-shaped male mold main body, and then connect the inner support 1-6 of the first core mold to the first male mold through the connecting element. ...
specific Embodiment approach 2
[0128] Specific implementation mode two: combination figure 1 To illustrate this embodiment, the pressure applied to the female mold 1-3 in step e of this embodiment is 0.75Mpa. Other compositions and connections are the same as in the first embodiment.
specific Embodiment approach 3
[0129] Specific implementation mode three: combination figure 1 To describe this embodiment, the curing temperature in step f of this embodiment is 150° C., and the curing time is 2 hours. Other compositions and connections are the same as those in Embodiment 1 or Embodiment 2.
PUM
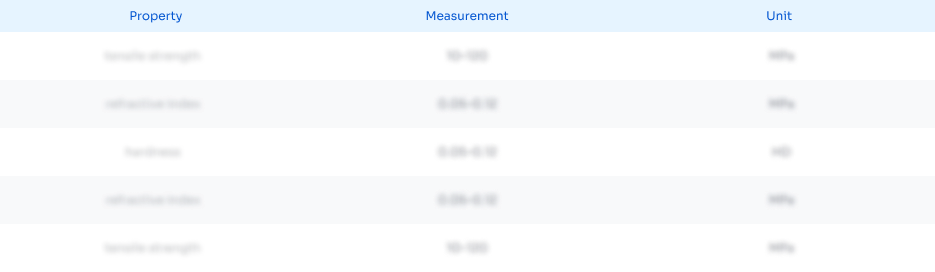
Abstract
Description
Claims
Application Information

- Generate Ideas
- Intellectual Property
- Life Sciences
- Materials
- Tech Scout
- Unparalleled Data Quality
- Higher Quality Content
- 60% Fewer Hallucinations
Browse by: Latest US Patents, China's latest patents, Technical Efficacy Thesaurus, Application Domain, Technology Topic, Popular Technical Reports.
© 2025 PatSnap. All rights reserved.Legal|Privacy policy|Modern Slavery Act Transparency Statement|Sitemap|About US| Contact US: help@patsnap.com