A high-precision multi-segmented hot-rolled steel bar graded controlled cooling process method
A process method and high-precision technology, applied in temperature control, rolls, manufacturing tools, etc., can solve problems such as increased demand for alloys, difficulty in controlling product size, and increased production costs
- Summary
- Abstract
- Description
- Claims
- Application Information
AI Technical Summary
Problems solved by technology
Method used
Image
Examples
Embodiment 1
[0021] A high-precision multi-segmented hot-rolled steel bar graded controlled cooling process method, comprising the following steps:
[0022] S1 heating furnace heating, the heating furnace adopts an automatic temperature control system, the billet gradually heats up through the preheating section, heating section, and soaking section and is fully soaked to ensure that the tapping temperature of the billet is within a certain range, and the overall temperature difference is ≤ 30 degrees Celsius;
[0023] The change of billet tapping temperature is as follows:
[0024] Preheating section Heating section soaking section billet tapping temperature temperature 800±50℃ 1000±50℃ 1150±50℃ 1030±20℃
[0025] S2 continuous rolling, 18 continuous rolling mills for rough, intermediate and finish rolling, 16 split stands for finish rolling, and between rough rolling and intermediate rolling mills, between intermediate rolling and finishing rolling mills, an...
Embodiment 2
[0039] A high-precision multi-segmented hot-rolled steel bar graded controlled cooling process method, comprising the following steps:
[0040] S1 heating furnace heating, the heating furnace adopts an automatic temperature control system, the billet gradually heats up through the preheating section, heating section, and soaking section and is fully soaked to ensure that the billet tapping temperature is within the range of 1050 ± 50 degrees Celsius, and the temperature difference throughout the body is ≤ 30 degrees Celsius ;
[0041] The change of billet tapping temperature is as follows:
[0042]
[0043]
[0044] S2 continuous rolling, 18 continuous rolling mills for rough, medium and finish rolling, 16 finishing stands for splitting;
[0045] S3K1 large-reduction rolling, K1 pass of finishing rolling adopts large-reduction and large-deformation rolling, and the deformation of the rolled piece is controlled in the range of 30%-40%, so as to deform and elongate the au...
PUM
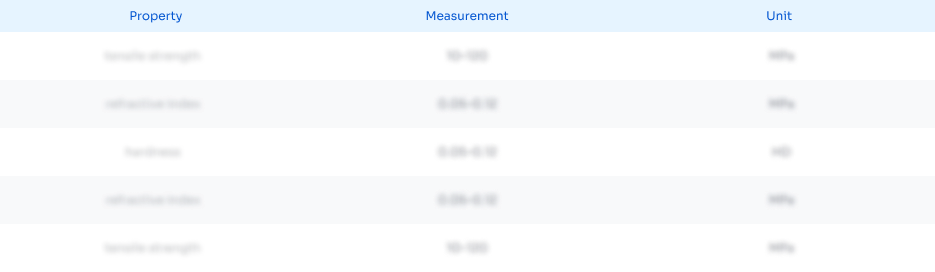
Abstract
Description
Claims
Application Information

- Generate Ideas
- Intellectual Property
- Life Sciences
- Materials
- Tech Scout
- Unparalleled Data Quality
- Higher Quality Content
- 60% Fewer Hallucinations
Browse by: Latest US Patents, China's latest patents, Technical Efficacy Thesaurus, Application Domain, Technology Topic, Popular Technical Reports.
© 2025 PatSnap. All rights reserved.Legal|Privacy policy|Modern Slavery Act Transparency Statement|Sitemap|About US| Contact US: help@patsnap.com