A preparation method for producing low-loss powder for integrated molding inductors
A low-loss, inductive technology, applied in the manufacture of inductors/transformers/magnets, circuits, electrical components, etc., can solve the problems of unsatisfactory improvement effects, singleness, and no comprehensive consideration, and achieve small anisotropic constants of magnetocrystals, High efficiency, the effect of improving efficiency
- Summary
- Abstract
- Description
- Claims
- Application Information
AI Technical Summary
Problems solved by technology
Method used
Examples
preparation example Construction
[0024] The invention provides a preparation method for producing low-loss powder for integrally formed inductors, comprising the following steps:
[0025] Mixed powder preparation: the mixed powder is made by mixing the first powder, the second powder and the third powder, wherein the first powder is carbonyl iron powder, D50 is 6-7um, and the mass percentage is 20-40 %, wherein the second powder is carbonyl iron powder, D50 is 3-4um, and the mass percentage is 30-40%, wherein the third powder is iron-silicon powder or amorphous powder, D50 is 10-15um, and the mass percentage is 30% ~40%; Among them, iron-silicon powder adopts iron-silicon 6.5 powder;
[0026] Phosphating treatment: take phosphoric acid at 0.1-1.5% of the mass of the mixed powder, take acetone at 5-10% of the mass of the mixed powder, dilute the phosphoric acid with the acetone evenly, add it to the mixed powder, and stir well After drying, bake at 60-80°C for 1-2 hours, and the phosphating treatment is compl...
Embodiment 1
[0037] Prepare 1000g of mixed powder, wherein the first powder is carbonyl iron powder of D50=6.1um, quality 300g, wherein the second powder is carbonyl iron powder of D50=3.1um, quality 350g, wherein the third powder is D50= 10.2um iron silicon 6.5 powder, mass 350g, mix the three powders evenly;
[0038] Take 2g of phosphoric acid and dilute it in 60g of acetone, add it into 1000g of mixed powder after dilution evenly, stir evenly, dry in the air, then bake at 60°C for 2 hours to obtain the mixed powder after phosphating treatment;
[0039]Take 12g of epoxy resin and 12g of silicone resin, dissolve them in 60g of acetone successively, dissolve them evenly, add them to the mixed powder after phosphating treatment, stir for 30 minutes to form a slurry, granulate, dry in the air, and then bake at 90°C Bake for 2 hours, add 2g of zinc stearate after natural cooling, stir evenly, and sieve to take 40-300 mesh as good product particles;
[0040] Take good product particles, press...
Embodiment 2
[0046] Prepare 1000g of mixed powder, wherein the first powder is carbonyl iron powder of D50=6.3um, quality 400g, wherein the second powder is carbonyl iron powder of D50=3.5um, quality 300g, wherein the third powder is D50= 12.3um iron silicon 6.5 powder, mass 300g, mix the three powders evenly;
[0047] Take 3g of phosphoric acid and dilute it in 80g of acetone, add it into 1000g of mixed powder after dilution evenly, stir evenly, dry in the air, then bake at 70°C for 2 hours to obtain the mixed powder after phosphating treatment;
[0048] Take 15g of epoxy resin and 15g of silicone resin, dissolve them in 80g of acetone successively, dissolve them evenly, add them to the phosphating-treated mixed powder, stir for 35 minutes to become a slurry, granulate, dry in the air, and then bake at 90°C Bake for 2 hours, add 3g of zinc stearate after natural cooling, stir evenly, and sieve to take 40-300 mesh as good product particles;
[0049] Take good product particles, press them...
PUM
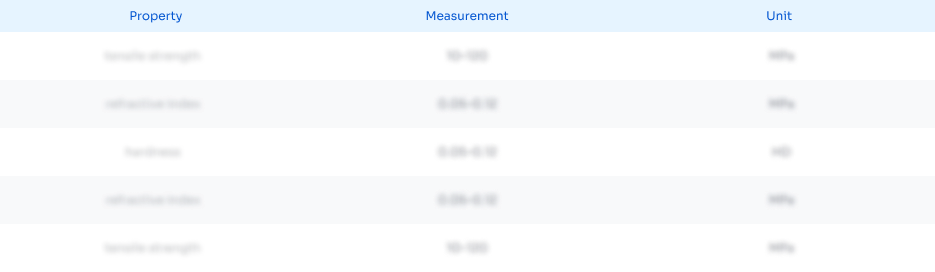
Abstract
Description
Claims
Application Information

- R&D Engineer
- R&D Manager
- IP Professional
- Industry Leading Data Capabilities
- Powerful AI technology
- Patent DNA Extraction
Browse by: Latest US Patents, China's latest patents, Technical Efficacy Thesaurus, Application Domain, Technology Topic, Popular Technical Reports.
© 2024 PatSnap. All rights reserved.Legal|Privacy policy|Modern Slavery Act Transparency Statement|Sitemap|About US| Contact US: help@patsnap.com