Direction adjustment control method and system for horizontal drilling machine
A technology of horizontal drilling rig and control method, which is applied to the automatic control system of drilling, drilling equipment and method, drilling equipment, etc. problems, to achieve the effect of reducing manual fatigue, fast tracking response, and reducing the degree of manual intervention
- Summary
- Abstract
- Description
- Claims
- Application Information
AI Technical Summary
Problems solved by technology
Method used
Image
Examples
Embodiment 1
[0043] See figure 1 , A horizontal drilling rig steering control system, including a positioning measurement system, a fuzzy controller, a PID controller, and a steering cylinder set on the drilling rig, the positioning measurement system is used to collect real-time position information of the drilling rig, the fuzzy control The device is used to receive the real-time angle and vertical deviation distance of the drilling rig, and load the PID controller parameters according to the set fuzzy control rules K P , K I with K D The PID controller sends an action signal to the corresponding direction adjustment cylinder according to the real-time PID parameters, and the direction adjustment cylinder component drives the drilling rig to adjust the direction through its own action, so that the drilling rig advances according to a predetermined route.
[0044] See figure 2 In this embodiment, the number of the steering cylinders is four groups and they are respectively arranged symmetric...
PUM
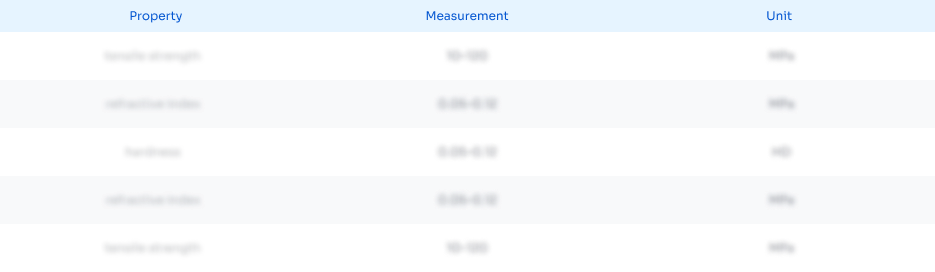
Abstract
Description
Claims
Application Information

- R&D Engineer
- R&D Manager
- IP Professional
- Industry Leading Data Capabilities
- Powerful AI technology
- Patent DNA Extraction
Browse by: Latest US Patents, China's latest patents, Technical Efficacy Thesaurus, Application Domain, Technology Topic, Popular Technical Reports.
© 2024 PatSnap. All rights reserved.Legal|Privacy policy|Modern Slavery Act Transparency Statement|Sitemap|About US| Contact US: help@patsnap.com