Continuous organic solid waste thermal hydrolysis treatment system and method
A technology for organic solid waste and treatment systems, applied in water/sludge/sewage treatment, sludge treatment, chemical instruments and methods, etc., can solve the problem of low system treatment efficiency and capacity, high cost per unit capacity, and reliability Insufficient durability and other problems, to achieve the effect of improving system processing capacity, low equipment cost, and easy steam absorption
- Summary
- Abstract
- Description
- Claims
- Application Information
AI Technical Summary
Problems solved by technology
Method used
Image
Examples
Embodiment 1
[0037] Such as figure 1 As shown, a continuous organic solid waste thermal hydrolysis treatment system includes a primary slurry reactor 1, a secondary slurry reactor group 2, a thermal hydrolysis reactor 3, a primary flash reactor 4 and a secondary stage flash reactor 5; the discharge port 15 of the primary slurry reactor 1 is connected to each secondary slurry reactor 14 in the secondary slurry reactor group 2 through the material delivery pump 12 The feed port 8 is connected, and there are at least two secondary slurry reactors 14 in the secondary slurry reactor group 2, and the outlet 15 of each secondary slurry reactor 14 is connected in parallel with the The feed port 8 of the thermal hydrolysis reactor 3 is connected, and the thermal hydrolysis reactor 3 is connected in series with the subsequent flash reactors in sequence.
[0038] The primary slurry reactor 1 is provided with a stirring device 6, the primary slurry reactor 1, the secondary slurry reactor 14, the ther...
Embodiment 2
[0051] Such as figure 1 As shown, a continuous organic solid waste thermal hydrolysis treatment system includes a primary slurry reactor 1, a secondary slurry reactor group 2, a thermal hydrolysis reactor 3, a primary flash reactor 4 and a secondary stage flash reactor 5; the discharge port 15 of the primary slurry reactor 1 is connected to each secondary slurry reactor 14 in the secondary slurry reactor group 2 through the material delivery pump 12 The feed port 8 is connected, and there are at least two secondary slurry reactors 14 in the secondary slurry reactor group 2, and the outlet 15 of each secondary slurry reactor 14 is connected in parallel with the The feed port 8 of the thermal hydrolysis reactor 3 is connected, and the thermal hydrolysis reactor 3 is connected in series with the subsequent flash reactors in sequence.
[0052] The primary slurry reactor 1 is provided with a stirring device 6, the primary slurry reactor 1, the secondary slurry reactor 14, the ther...
PUM
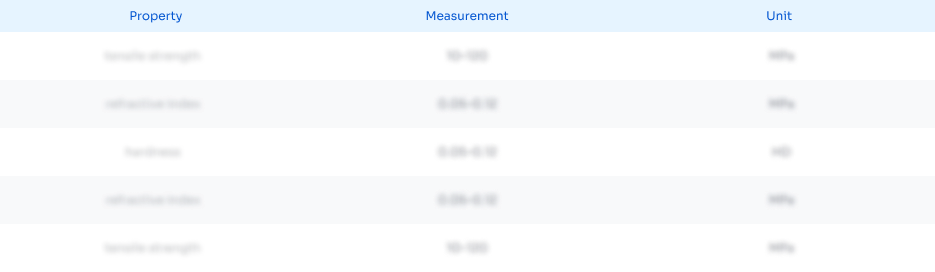
Abstract
Description
Claims
Application Information

- R&D
- Intellectual Property
- Life Sciences
- Materials
- Tech Scout
- Unparalleled Data Quality
- Higher Quality Content
- 60% Fewer Hallucinations
Browse by: Latest US Patents, China's latest patents, Technical Efficacy Thesaurus, Application Domain, Technology Topic, Popular Technical Reports.
© 2025 PatSnap. All rights reserved.Legal|Privacy policy|Modern Slavery Act Transparency Statement|Sitemap|About US| Contact US: help@patsnap.com