Micro-capsule calcium chloride for dairy cows as well as preparation method and application thereof
A technology of microencapsulated calcium chloride and calcium chloride, which can be used in applications, molding or processing of animal feed, animal husbandry, etc., and can solve the problems of primary coating particle damage, long production process, and invalid primary coating, etc. problems, to achieve the effect of improving moisture absorption, low production energy consumption, and improving bioavailability
- Summary
- Abstract
- Description
- Claims
- Application Information
AI Technical Summary
Problems solved by technology
Method used
Image
Examples
Embodiment 1
[0040] Embodiment 1, prescription screening
[0041] Investigate two main indicators: in vitro dissolution and moisture resistance.
[0042] 1. In vitro dissolution of microencapsulated calcium chloride
[0043] The pH of the rumen of dairy cows is between 6.2 and 6.8, the pH of the abomasum of dairy cows is about 1.2 when they are fasting, and about 4.3 when they are full. Choose pH 6.8 phosphate buffer to simulate rumen environment, and pH 1.2 and 4.3 to simulate dairy cow abomasum environment.
[0044] The reagents used are as follows:
[0045] In vitro simulated abomasal juice Ⅰ, i.e. hydrochloric acid solution with pH = 1.2, accurately measure 425mL of 0.2mol / L hydrochloric acid solution, dilute with water to 1000mL, shake well, and obtain;
[0046] In vitro simulated abomasal juice II, that is, acetic acid buffer solution with pH=4.3, accurately weigh 1.99g of sodium acetate and place it in a 1000mL volumetric flask, add water to dissolve it, add 17.7mL of 2mol / L acet...
Embodiment 2
[0075] Embodiment 2, prepare microcapsule calcium chloride
[0076] Put 186kg of hydrogenated oil into a jacketed heating tank to melt, control the jacket temperature to 100°C, transfer the melted hydrogenated oil to the dispersion stirring tank, maintain the jacket temperature of the dispersion stirring tank at 80°C, start the mixer, and gradually add 18kg glyceryl monostearate, 96kg calcium chloride raw material (calcium chloride content is 93.6wt%), after stirring, start shearing machine, homogenizer, make material mixing and homogeneous emulsification, obtain compound, then The mixture is sent to the centrifugal spray tower, the inlet air temperature of the centrifugal spray tower is controlled to be less than or equal to 5°C, the speed of the centrifugal turntable is 3000r / min, and the air volume is 30000m 2 / min to obtain microencapsulated calcium chloride granules, sieve them with a vibrating sieve, collect microencapsulated calcium chloride granules with a particle dia...
Embodiment 3
[0078] Embodiment 3, prepare microcapsule calcium chloride
[0079] Put 153kg of hydrogenated oil into the jacketed heating tank to melt, control the jacket temperature to 100°C, transfer the melted hydrogenated oil to the dispersion stirring tank, maintain the jacket temperature of the dispersion stirring tank at 80°C, start the mixer, and gradually Add 18kg glyceryl monostearate, 129kg calcium chloride raw material (calcium chloride content is 93.6wt%), start shearing machine, homogenizer after stirring evenly, make material mixing and homogeneous emulsification, obtain compound, then The mixture is sent to the centrifugal spray tower, and the air inlet temperature of the centrifugal spray tower is controlled to be less than or equal to 5°C, the speed of the centrifugal turntable is 3000r / min, and the air volume is 30000m 2 / min to obtain microencapsulated calcium chloride granules, sieve them with a vibrating sieve, collect microencapsulated calcium chloride granules with a...
PUM
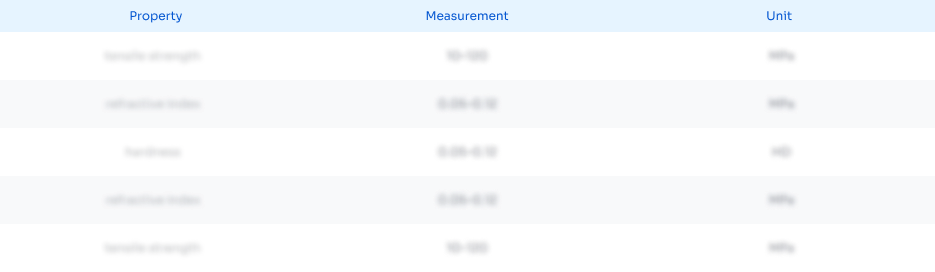
Abstract
Description
Claims
Application Information

- Generate Ideas
- Intellectual Property
- Life Sciences
- Materials
- Tech Scout
- Unparalleled Data Quality
- Higher Quality Content
- 60% Fewer Hallucinations
Browse by: Latest US Patents, China's latest patents, Technical Efficacy Thesaurus, Application Domain, Technology Topic, Popular Technical Reports.
© 2025 PatSnap. All rights reserved.Legal|Privacy policy|Modern Slavery Act Transparency Statement|Sitemap|About US| Contact US: help@patsnap.com