Dynamic error compensation and control method of cutting machining robot
A dynamic error and control method technology, applied in computer control, program control, general control system, etc., can solve the problems of low repeat positioning accuracy, limit robot application, cumbersome analysis and control, etc., achieve excellent control performance and suppress high-precision , to achieve the effect of compensation and control
- Summary
- Abstract
- Description
- Claims
- Application Information
AI Technical Summary
Problems solved by technology
Method used
Image
Examples
Embodiment 1
[0067] This embodiment proposes a dynamic error compensation and control method for a cutting robot. The dynamic errors of this method include three types: stable deformation error, low-frequency vibration error, and high-frequency vibration error. The specific implementation of this method is:
[0068] A) when the dynamic error is a stable deformation error, error compensation and control are performed based on the offline compensation module 6 and the online correction module 7;
[0069] B) When the dynamic error is a low-frequency vibration error, an open-loop control method based on modal analysis is used to offset the excitation force of the low-order mode by applying an additional active force at the robot joint, thereby suppressing the vibration and performing error compensation and control;
[0070] C) When the dynamic error is a high-frequency vibration error, a robot dynamics control algorithm based on a parameter self-correction and self-disturbance rejection strat...
PUM
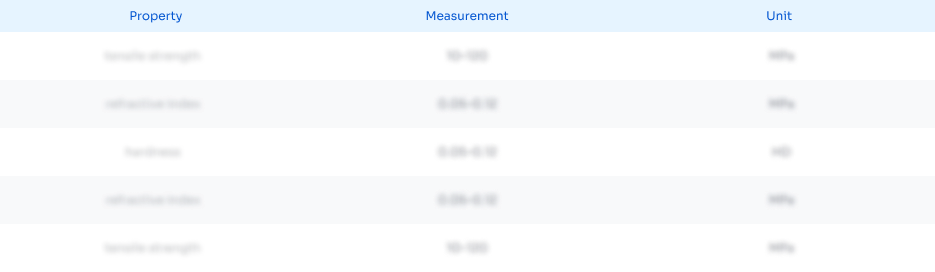
Abstract
Description
Claims
Application Information

- R&D Engineer
- R&D Manager
- IP Professional
- Industry Leading Data Capabilities
- Powerful AI technology
- Patent DNA Extraction
Browse by: Latest US Patents, China's latest patents, Technical Efficacy Thesaurus, Application Domain, Technology Topic, Popular Technical Reports.
© 2024 PatSnap. All rights reserved.Legal|Privacy policy|Modern Slavery Act Transparency Statement|Sitemap|About US| Contact US: help@patsnap.com