A U-shaped workpiece automatic welding tracking system and working method based on Leisai controller
A tracking system and working method technology, applied in welding equipment, manufacturing tools, welding equipment, etc., can solve the problems of inaccurate welding point search, high algorithm complexity, reduced measurement accuracy, etc., to ensure timeliness and high real-time performance. , The effect of improving welding accuracy and efficiency
- Summary
- Abstract
- Description
- Claims
- Application Information
AI Technical Summary
Problems solved by technology
Method used
Image
Examples
Embodiment 1
[0059] A U-shaped workpiece automatic welding tracking system based on the Leisai controller, including: a four-axis welding tracking system, a mechanical arm and a welding torch, the four-axis welding tracking system is set on the mechanical arm, and the welding torch is set on the mechanical arm , wherein the four-axis welding tracking system is provided with a laser position sensor 1, a controller 2, a set of mechanical arm control mechanisms 3 for controlling the operation of the mechanical arm, a set of control mechanisms for controlling the up and down movement of the welding torch and the adjustment of the rotation angle The welding torch control mechanism 4 and the display screen 5, the output end of the laser position sensor 1 is connected with the input end of the controller 2, and the output end of the controller 2 is simultaneously connected with the input end of the mechanical arm control mechanism 3 and the welding torch control mechanism 4, and the display screen...
Embodiment 2
[0064] A U-shaped workpiece automatic welding tracking system based on the Leisai controller, including: a four-axis welding tracking system, a mechanical arm and a welding torch, the four-axis welding tracking system is set on the mechanical arm, and the welding torch is set on the mechanical arm , wherein the four-axis welding tracking system is provided with a laser position sensor 1, a controller 2, a set of mechanical arm control mechanisms 3 for controlling the operation of the mechanical arm, a set of control mechanisms for controlling the up and down movement of the welding torch and the adjustment of the rotation angle The welding torch control mechanism 4 and the display screen 5, the output end of the laser position sensor 1 is connected with the input end of the controller 2, and the output end of the controller 2 is simultaneously connected with the input end of the mechanical arm control mechanism 3 and the welding torch control mechanism 4, and the display screen...
Embodiment 3
[0074] A U-shaped workpiece automatic welding tracking system based on the Leisai controller, including: a four-axis welding tracking system, a mechanical arm and a welding torch, the four-axis welding tracking system is set on the mechanical arm, and the welding torch is set on the mechanical arm , wherein the four-axis welding tracking system is provided with a laser position sensor 1, a controller 2, a set of mechanical arm control mechanisms 3 for controlling the operation of the mechanical arm, a set of control mechanisms for controlling the up and down movement of the welding torch and the adjustment of the rotation angle The welding torch control mechanism 4 and the display screen 5, the output end of the laser position sensor 1 is connected with the input end of the controller 2, and the output end of the controller 2 is simultaneously connected with the input end of the mechanical arm control mechanism 3 and the welding torch control mechanism 4, and the display screen...
PUM
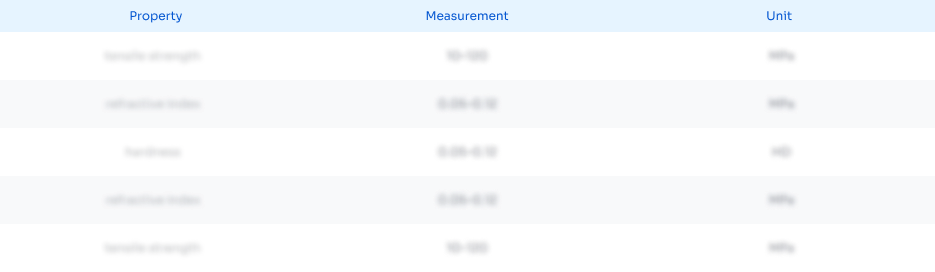
Abstract
Description
Claims
Application Information

- Generate Ideas
- Intellectual Property
- Life Sciences
- Materials
- Tech Scout
- Unparalleled Data Quality
- Higher Quality Content
- 60% Fewer Hallucinations
Browse by: Latest US Patents, China's latest patents, Technical Efficacy Thesaurus, Application Domain, Technology Topic, Popular Technical Reports.
© 2025 PatSnap. All rights reserved.Legal|Privacy policy|Modern Slavery Act Transparency Statement|Sitemap|About US| Contact US: help@patsnap.com