Double-AGV cooperative carrying control system and method
A control method and deviation technology, applied in the field of intelligent industrial robots, can solve problems involving only
- Summary
- Abstract
- Description
- Claims
- Application Information
AI Technical Summary
Problems solved by technology
Method used
Image
Examples
Embodiment Construction
[0046] The specific embodiments of the present invention will be further described below in conjunction with the accompanying drawings.
[0047] A dual AGV cooperative carrying control method, which consists of two omni-directional mobile AGV front and rear layouts. On the basis of referring to the existing multi-agent formation control method, a heterogeneous pilot-follow method is adopted, combined with visual guidance path tracking method, constructing a cooperative control model of a three-layer topology structure, and establishing a dual AGV kinematics control model under path tracking and pilot-following based on path deviation and formation deviation, and adopting a rolling predictive control based on time domain The discrete control model optimizes the kinematics control model to realize the stable and reliable cooperative operation of the dual AGV system.
[0048] combined with figure 1 , in the dual AGV cooperative carrying control method described in the present in...
PUM
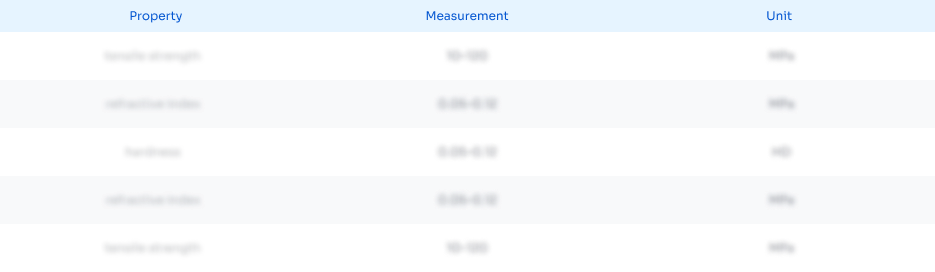
Abstract
Description
Claims
Application Information

- Generate Ideas
- Intellectual Property
- Life Sciences
- Materials
- Tech Scout
- Unparalleled Data Quality
- Higher Quality Content
- 60% Fewer Hallucinations
Browse by: Latest US Patents, China's latest patents, Technical Efficacy Thesaurus, Application Domain, Technology Topic, Popular Technical Reports.
© 2025 PatSnap. All rights reserved.Legal|Privacy policy|Modern Slavery Act Transparency Statement|Sitemap|About US| Contact US: help@patsnap.com