Aircraft wing rib and production process thereof
A production process and rib technology, applied in the directions of wings, aircraft assembly, aircraft parts, etc., can solve the problems of rib fracture, low structural strength, slow flow rate, etc.
- Summary
- Abstract
- Description
- Claims
- Application Information
AI Technical Summary
Problems solved by technology
Method used
Image
Examples
Embodiment 1
[0067] refer to figure 1 , is an aircraft wing rib disclosed by the present invention, comprising a trapezoidal rib 1 and a support plate 2 fixedly connected to the edge of the rib 1, and one side of the rib 1 is fixedly connected with a plurality of criss-cross reinforcements 3 A mounting plate 4 is obliquely and fixedly connected to the edge of the side of the rib plate 1 away from the reinforcing member 3 . In this embodiment, the entire wing rib is preferably made of 7050-T7451 aluminum alloy material, and is cut into a specific shape by a CNC machining center, so all connection methods in this embodiment are integrally formed and fixedly connected.
[0068] The main alloying element of 7075 series aluminum alloy is zinc. Adding magnesium to the alloy containing 3%-75% zinc can form MgZn2 with significant strengthening effect, making the heat treatment effect of the alloy far better than that of aluminum-zinc binary alloy. Increasing the zinc and magnesium content in the ...
Embodiment 2
[0078] refer to image 3 , a production process for aircraft wing ribs, comprising the steps of:
[0079] Step S1: Design the macroscopic shape and microscopic structural parameters of the wing ribs through drawing software, and then transmit the data to the console of the CNC machining center through the computer.
[0080] Step S2: According to the raw materials provided by the warehouse, verify the furnace batch number, sawing material and quality inspection of the raw materials, and mark them on the raw materials.
[0081] In step S2, the raw material is preferably 7050-T7451 aluminum alloy plate, 7050-T7451 aluminum is a high-strength heat-treatable alloy with extremely high strength and resistance to exfoliation corrosion and stress corrosion cracking. The blank size is 650*430*88.9MM, 25.6*17*3.5IN, and the saw size is 590*410*88.9MM, 23.22*16.14*3.5IN. After precise sawing on the blank, the preliminary shape of the product is obtained, which is convenient for subseque...
PUM
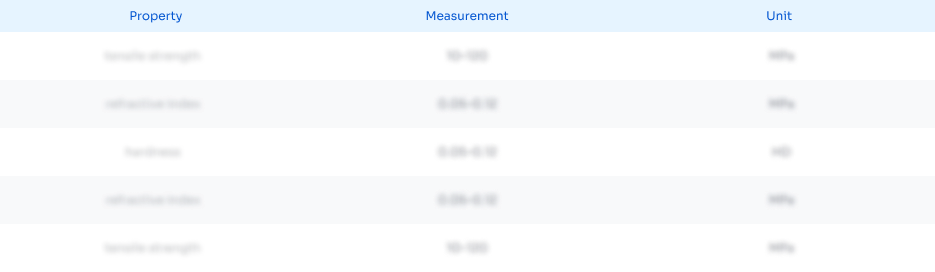
Abstract
Description
Claims
Application Information

- R&D
- Intellectual Property
- Life Sciences
- Materials
- Tech Scout
- Unparalleled Data Quality
- Higher Quality Content
- 60% Fewer Hallucinations
Browse by: Latest US Patents, China's latest patents, Technical Efficacy Thesaurus, Application Domain, Technology Topic, Popular Technical Reports.
© 2025 PatSnap. All rights reserved.Legal|Privacy policy|Modern Slavery Act Transparency Statement|Sitemap|About US| Contact US: help@patsnap.com